品牌:荣森
起订:1套
供应:100套
发货:60天内
信息标签:天然石膏脱硫生产线烟气脱硫脱硝除尘煅烧设备,供应,机械及行业设备,化工设备
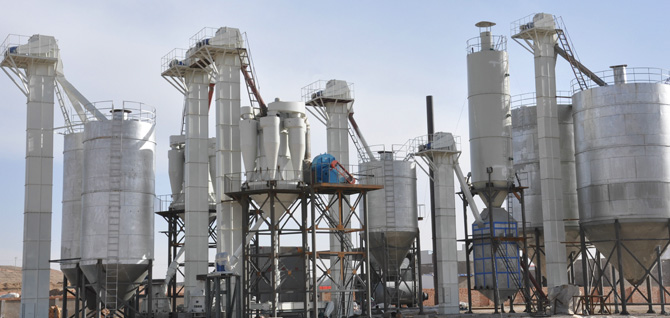
工艺流程:原料→破碎→提升机1→生料仓→外烧式煅烧炉→提升机2→冷却室→提升机3→熟料仓→粉磨→提升机4→成品仓→包装
从原料破碎到成品包装,整套系统处于密闭的负压状态。收尘系统采用4级布袋除尘,使在生产工程中出现的烟气、水蒸气、粉尘等污染源得到充分的处理,厂房内外无扬尘出现,排放达到30mg/m3的标准,**解决了粉尘治理的难题。
1进料系统
天然石膏原料通过铲车送入下料斗(下料斗规格:4×3×2米),然后进入振动筛,使石膏粉原料能够均匀的进入破碎机。振动筛是间歇式工作,一般是每工作10秒停止5秒。振动筛规格:长3×宽1米,功率7.5kw。
2破碎系统
破碎机我们选用60-100型号锤式破碎。该破碎机功率为30kw,破碎石膏至0.5mm以下的微小颗粒和面状,每小时可破碎20吨。破碎后的石膏粉经过1号提升机进入原料仓,原料仓容量50T,能满足破碎机2.5小时的生产任务。1号提升机高度16米,功率5.5kw,原料仓高度14m、直径2.6m。在进行破碎的同时,会产生大量的粉尘。为避免这种污染及浪费,我们采用布袋除尘器对粉尘进行回收利用。
3外烧式回转窑煅烧系统
石膏从原料仓通过电磁给料机进入螺旋进料器,螺旋进料器放在煅烧炉的中心位置,均匀的把原料送进煅烧炉内部进行煅烧。外烧式回转窑煅烧炉规格:直径2.2米×20米,传动电机功率30kw6级,减速机750型,采用齿圈传动,保证运行平稳。热源直接作用于回转窑外壁,正常外壁温度达到400-600摄氏度,回转窑内部布置了一周圈的加热管,增加30%的加热面积,大大降低了生产成本。回转窑外部整体用耐火砖砌成,两端留有进出料口,在回转窑和外部耐火砖接触的部位,我们采用片式密封,既起到保温增产的功效,又起到了环保效益。供热系统采用烧煤机自动进煤燃烧,并配备22kw高压风机,确保煤的充分燃烧,利用率提高10%。对于高温烟气的处理,选用HMD240高温布袋式除尘器,该除尘器**高耐温度180℃使用成本低,效果好,处理烟气达到国家排放标准。
4冷却系统
对于煅烧好的石膏粉,这时的表面温度达到150℃以上。如果直接进行粉磨,会把热量出递给钢磨,影响钢磨及箩底的使用寿命。所以必须对刚煅烧好的石膏粉进行降温冷却处理。降温处理我们采用科学的塔式自动冷却处理方式,把温度降低到原有温度的50%后,再进入熟料仓备用粉磨。
5粉磨系统
石膏粉经过降温冷却后,从冷却室出料口经过3号提升机,再通过FU输送机进入熟料仓。熟料仓和原料仓规格相同,均使用容量为50T的仓体。石膏粉在熟料仓底部通过定量器,进入磨机粉磨。磨机型号增利牌500型钢磨,每台功率18.5kw,粉体细度100目左右,共需3台。
6成品包装系统
石膏粉从粉磨好后经过3号提升机进入成品仓。成品仓容积250立方左右,可容纳100T左右。高度20米,直径4米,共2座。提升机高度22米,功率15kw。成品仓底部配备自动装包机,可进行连续包装,或根据需要随时进行包装。
7电气控制系统
从石膏原料的破碎一直到成品包装,每一个电器的控制均在配电室内操作。配电室共5组配电柜,1号柜是进线柜,2、3、4、5分别是电气控制柜。自动化程度高,操作简单易懂,安全可靠。
8除尘系统
整套生产线为全封闭结构,生产过程中不会有粉尘外泄。共采用四组分段式布袋除尘工艺,具体细分为破碎阶段除尘HMD96、煅烧阶段除尘HMD240、粉磨阶段除尘HMD160、成品仓阶段除尘HMD36。
除尘布袋材质为亚克力覆膜滤袋,亚克力覆膜滤袋广泛用于冶金、电力、垃圾焚烧、沥青搅拌站、化工、水泥等高温烟气行业的通风除尘和物质回收,除尘效率可达99.99%。经过处理后的空气粉尘含量小于30mg/m3,完全符合国家排放标准。