9A SOLID FILM LUBRICANT
HEAT CURING
SERIES E750
MEETS SAE SPEC AS5272C Type II
FORMERLY MIL-L-46010D TYPE II
TECHNICAL INFORMATION GUIDE
.
Lubricative Pigment Molybdenum Disulfide
Color Flat Dark Gray
Shelf Life 1 year from date of Manufacture
Vacuum Outgassing None @ 10-6 Torr.
Lox Compatibility 100% compatible and shock resistant
Resistivity 1.4 x 106 OHMS CM
Coefficient of Friction 0.0236 (Falex Test)
Load Carrying Capacity 2250 lbs. ASTM D2625 B
Corrosion Protection OVER 1500 hours* ASTM B117
(@ .0005" DFT on DoD-P-16232 Type M
Class 3 phosphated steel)
*Test halted before failure occurred
COMPOSITION AND PHYSICAL PROPERTIES
DEs
criptION
Sandstrom 9A Dry Film Lubricant is a paint-like coating
co
ntaining molybdenum disulfide and corrosion inhibiting
pigments. This Heat Curing material prevents corrosion,
galling, seizing, and fretting. It is a low-friction coating which
exhibits long wear life when operated at -3200F to +5000F
under loads exceeding 100,000 psi.
9A should be applied wher maximum wear life and corrosion
protection from a dry film lubricant are required.
o
nce Sandstrom 9A has been heat cured, it is virtually
unaffected by atmospheric and fretting corrosion, solvents,
acids, oils, degreasers, and is not resoftened again at elevated
temperatures.
9A can be applied to a wide variety of surfaces by spraying
or dipping. Complete application instructions are on the
reverse of this sheet.
OUTSTANDING FEATURES/BENEFITS
Excellent Corrosion Protection, Chemical Resistance, and
Long Wear Life are its outstanding characteristics.
SANDSTROM 9A Co
nTAINS NO GRAPHITE
Use Sandstrom "099" as an alternative to 9A wher low VOC
and no lead is preferred. 099's performance is comparable
to 9A.
TYPICAL USES
Sandstrom 9A is an excellent solution to the problem of lubricating
parts:
• That will be operated in corrosive atmospheres
• That may be stored for long periods
• Which are seldom lubricated o
nce they leave the factory and
wher permanent lubrication is desired
• wher operating pressures exceed the load-bearing capaci ties
of ordinary oils and greases
• wher "clean operation" is desired (9A will not collect dirt and
debris like grease and oils)
• wher a protective coating and sacrificial break-in lubricant
is needed
• wher fretting and galling is a problem (such as splines,
universal joints, and keyed bearings)
• wher easy release is desired (such as fasteners and PVC
molds)
• wher parts may be subjected to frequent disassembly
Net Wt./ Gallon 9.5 lbs. + .2 lb.
Solids Co
ntent 40% minimum (By Wt.)
Viscosity 40 - 46 sec (#1 Zahn cup @ 770F)
Flash Point 440F+ 20F Setaflash
Operating Temp. Range -3200F to +5000F
Vehicle Type Epoxy-Phenolic
VOC 5.5578 lbs./gal. minus water
(Theoretical)
Specifications: SAE Spec AS5272C
PRI QPL AS5272 type 2
Wear Life: 496 Minutes average
ASTM D2625 A
NOTICE
Before using this product, read all warnings and safety
information printed on the label, the Material Safety da
ta
Sheet, and the Technical Info-Guide
STIRRING
im
portANT! THIS LUBRICANT Co
nTAINS HEAVY PIGMENTS
WHICH SETTLE RAPIDLY. THEREFORE, IT SHOULD BE
STIRRED THOROUGHLY BEFORE USE AND CONTINUOUSLY
DURING APPLICATION.
THINNING
For spraying* - Use 2 parts 9A to 1 part PM solvent.
For dipping* - Use slow-drying thinner mixture of PM and PMA,
blended 1:1, as to provide proper run-off characteristics. The
suggested starting point is 4 parts 9A to 1 part thinner mixture.
*By volume.
APPLICATION
SANDSTROM 9A should be sprayed or dipped to the desired film
thickness (usually .0003 to .0007 inches). Allow parts to flash off at
least 30 minutes at 770F +50F.
BAKING
BAKING 4000F (2040C) FOR ONE (1) HOUR in a forced draft oven
will yield optimum corrosion protection and wear life.
im
portANT! The hour begins when the part has reached 4000F
(2040C), NOT when it is placed in the oven. In cases of very thick
me
tals, an extra hour may be required to bring the part up to the
proper temperature. Thermocouples may be used to determine
the true temperature of the me
tal. However, if the me
tallurgical
properties are adversely affected by baking at this temperature
(i.e., ALUMINUM, in some cases), we would recommend use of
SANDSTROM LC-300 Heat Curing Lubricant which cures at 3000F
(1490C) in ONE (1) HOUR. SANDSTROM 099 could also be used
as it will cure in temperatures ranging from 3000F to 4000F.
IT IS IMPERATIVE TO USE A PROPERLY VENTED OVEN (DIRECT
VENT TO THE OUTSIDE).
CLEANUP
Use the same solvents for cleaning tools as are recommended for
thinning.
REMOVAL OF SANDSTROM 9A
In the event it is necessary to remove Sandstrom 9A, physical
removal is best (such as grit blasting, sanding, or grinding).
**Strict compliance to the instructions given in Surface
Treatment, Stirring, and Baking is essential to obtain
optimum results.
WARNINGS: Co
nstant stirring is imperative for best results.
Caution: Flammable. Keep away from sparks and open flame.
Use with adequate ventilation. Avoid prolo
nged breathing of
vapors. If swallowed--DO NOT INDUCE VOMITING. Contains
Toluene and Phenolic and Epoxy Resins. Call physician immediately.
GENERAL
Sandstrom 9A is a paint-like material co
nsisting of lubricative pigments
dispersed in a thermosetting resin system thinned with appropriate solvents.
For maximum service, the APPLICATION INSTRUCTIONS MUST BE
FOLLOWED CLOSELY. The lubricant
is flammable and the safety precautions usually followed when using
flammable materials must be observed.
FILM THICKNESS AND ENGINEERING TOLERANCES
As supplied, SANDSTROM 9A will yield a film thickness of a
bout .0005
inches per dip coat. Usually engineering tolerances will permit necessary
minimum film buildup of .0002 to .0003 inches without interference. If excess
buildup does occur and a force fit is necessary, burnishing lightly will assist
in mating the parts. The remaining excess will be worn away in the first few
cycles of operation. Whenever possible, the proper tolerances should be
designed into the part.
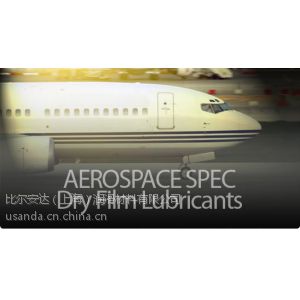
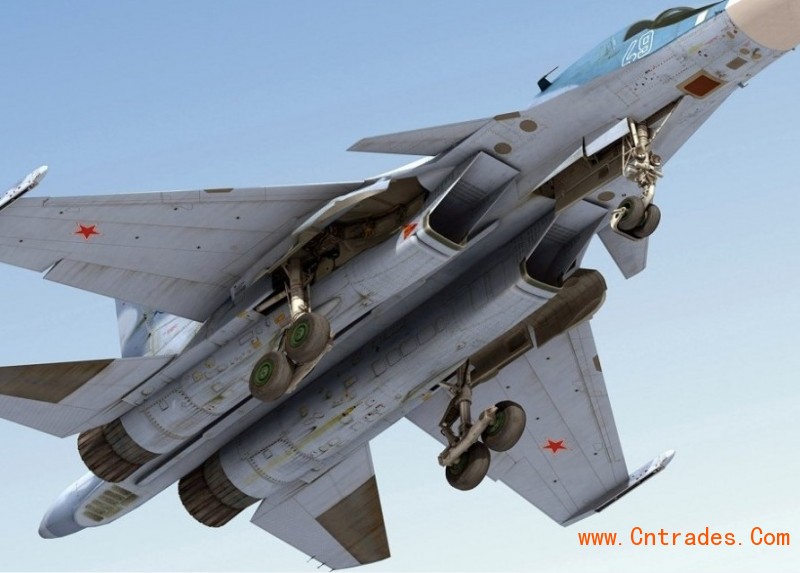