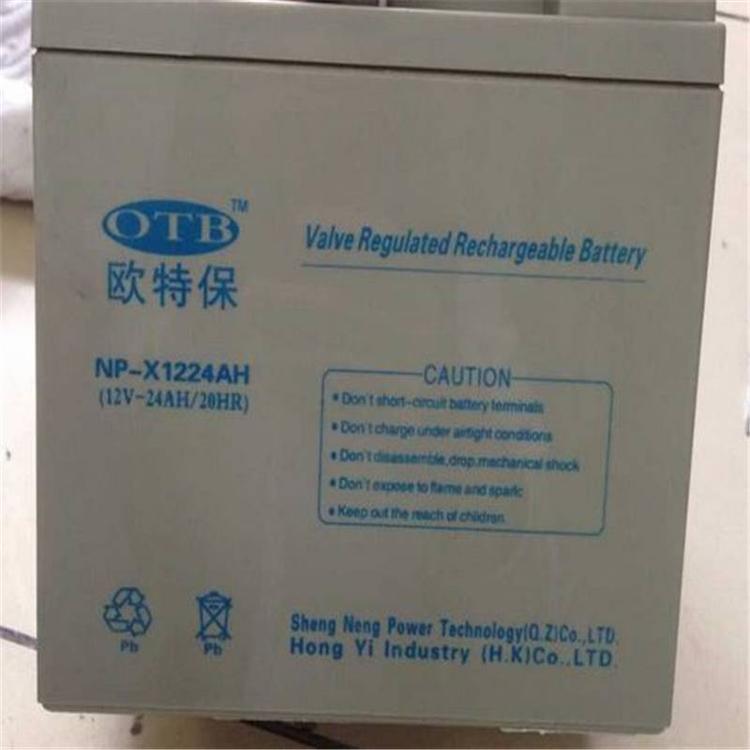
OTB蓄电池用途:UPS不间断电源 应急照明系统
铁路、航运、交通 电厂、变电站、核电站
消防安全报警系统 无线通讯系统、程控交换机、移动通讯
太阳能储存能量转换设备 控制设备及其紧急保护系统、个人计算机
维护简单: 欧特保系列的电池是真正意义上的免维护电池,在正常使用寿命期内,无需补水或稀酸,不会发生电解液干涸。
OTB蓄电池12V系列蓄电池是普通阀控式密封铅酸蓄电池,设计浮充使用寿命4-6年(20°C )。CB系列产品具有使用安全、可靠、不漏液,可立放、卧放使用,运输、安装方便,适用温度范围广,维护简单,在正常使用寿命期间无需加蒸馏水或电解液等特点。适合于UPS 、EPS等紧急备用电源设备和不间断电源设备。
维护简单: 欧特保系列的电池是真正意义上的免维护电池,在正常使用寿命期内,无需补水或稀酸,不会发生电解液干涸。OTB蓄电池技术参数
安全性高:欧特保系列的电池在正确使用过程电池内部或外部遇到明火不会发生 自燃和破裂,安全性高。
可靠性好:欧特保系列电池在出厂前通过负荷测试(检验密合度、内阻、开路电压、闭路电压),保证所有出厂电池无漏液、性能不良等情况。
一致性好:欧特保系列电池在出厂前通过充放电循环,并根据客户要求严格进行筛选配组,保证电池间一致性较好,特别适合于UPS选用。
寿命长:欧特保系列电池采用特殊的铅钙多元素合金设计独特的生产工艺,使产品在浮充使用和循环使用时都有很长的寿命。
高倍率放电性能好:欧特保系列电池采用特殊的设计从而大大改善了产品的高倍率放电性能,可以使用于大电流深放电。
欧特保OTB蓄电池NP-X127AH参数报价作为工程技术中心的依托企业,长兴县本土企业超威集团经过长期技术攻关,研究出了能够解决铅蓄电池生产环节污染问题的无镉内化技术,获得了生产铅蓄电池的“绿色通行证”。
据超威集团研究院院长刘孝伟介绍,无镉内化成工艺取消了传统的外化技术的极板化成工序,也取消了对极板的充电、水洗、抗氧化处理和2次干燥,简化了工艺操作,节省了大量的工时和能源消耗,降低了劳动强度,减少了员工人数的15%;通过运用铅钙合金新配方解决了蓄电池生产中无害化配方的行业技术难题,降低了电池生产成本,减少了酸雾和废水的排放量。不仅大大降低了企业环保治理的费用,而且有效提高了产品的一致性,使电池质量明显提高。
“无镉内化成工艺和传统外化成相比减少用水90%、节电28.5%,降低成本15%,减少酸雾排放强度50%以上,每只6-DZM-12AH电池可减少综合成本0.8到1元。内化去镉既有利于企业,有利于环境,更有利于消费者。超威集团现在每年可节约工业用水400万吨,如果无镉内化技术能在电池行业中推广,每年可减少重金属废水排放900多万吨,减少重金属铅排放9吨以上;同时减少重金属污水处理费投入近10亿元,间接效益和直接效益达15亿元,对我国铅蓄电池行业的清洁化生产与环保节能减排以及整个行业的绿色发展具有十分重要的推动与促进作用。”刘孝伟说。
在铅蓄电池回收再利用环节,超威集团探索出了“原子经济法”,让废旧的铅蓄电池中的铅变成可用原料,实现就地回收,就地生产。
超威集团董事长周明明介绍,原子经济法铅回收是与当前国内外废旧铅酸蓄电池“热处理”和“湿处理”截然不同的一种全新回收方法,通过原子经济反应,用化学方法将废铅蓄电池转化成可直接利用的铅粉,处理过程中无烟尘、废气、废水排放,产生的废渣为传统工艺的5%到10%,回收利用率达99%以上,能耗仅为传统工艺的50%,实现了废旧蓄电池回收流程由高能耗、低回收、高污染的复杂流程向低能耗、高回收、低污染的绿色流程转变。
“项目正在‘提速换挡’,从日产10千克氧化铅粉的试产到日产氧化铅粉200千克,目前正在设计年回收5万吨废旧铅蓄电池生产线,目标是建成全球首条废旧蓄电池回收高值利用示范线。”周明明说。技术规模难题待解
虽然前景一片光明,但动力电池回收尚处起步阶段,规模、技术方面仍存诸多难点。
“动力电池回收市场亟待形成对电池全生命周期的信息溯源系统,同时,设计标准、市场定价目前还都没有形成规范。”夏诗忠表示,退役动力电池具有资源化属性,但回收市场监管不严,回收渠道众多,所以市场价格混乱而不透明,造成恶性竞争,不能有效保证合法合规的回收企业成本上的竞争力。目前,市场未建立有效的动力电池回收模式,整体处于无序状态,不具规模。电池极易流入个体私营者、零售商、汽车维修店等非专业回收利用机构,造成资源浪费、环境二次污染等,增加了专业回收利用企业的收购成本,阻碍企业规模化发展。更有甚者,将回收的动力电池经简单处理后再次流人市场,严重危害人身道路安全。
他表示,由于废旧动力电池拆解具有一定的危险性,而目前报废的前期动力电池没有统一的编码和尺寸的标准,因此自动化拆解难度较大。此外,各地的产业政策不完善,加之一些没有技术保证和社会责任感的中小企业粗暴回收废旧动力电池,导致有价金属回收效率低,污染排放重,使整个锂电回收行业受到地方政府和环保部门的误解。
其称,目前行业急需对汽车主机厂、电池供应商、第三方电池回收企业都公开的动力电池全生命周期信息溯源系统,根据退役电池的基本数据快速判断动力电池的剩余容量和原材料构成,方便动力电池重组梯次利用和分类回收处理。同时,对于动力电池结构设计标准需要统一,并且从电池模组开始引入模块化、易拆解的设计,便于拆解与重组。
除行业规范性缺失,技术难点众多外,高企的工艺成本,也使得动力电池回收企业的盈利状况不容乐观。
中信证券研报称,当前动力电池回收的各参与方大多数都处于示范项目或者微盈利经营状态,而形成规模效应、降 低成本是当下动力电池回收的重要突破点。鉴于目前动力电池回收的规模和体量还都较小,随着行业规范性不断提升,以及龙头企业不断布局带动产业升级加速的规模效应,成本端压力会在未来行业逐渐发展的过程中消减。
格林美董秘欧阳铭志此前也对外表示,拆解回收存在的主要问题在于难以形成规模化效应,梯次利用也存在技术不成熟、处理成本高等问题。在2018年之前,由于新能源汽车的动力电池还未进入报废端,可供回收利用的电池十分有限,导致企业难以实现批量化的回收利用。
“锂离子电池回收技术路线比较复杂,回收工艺成本高。而除三元系正极回收价值高外,像锰酸锂、磷酸铁锂系等正极回收价值均偏低。”夏诗忠也表示,高额的税收,日益增长的环保处理成本,政策执行不到位,激励机制的缺失对动力电池回收行业的商业可行性构成了很大挑战,回收企业唯有规模化发展才能带来盈利空间。
规模化发展有望破局
动力电池回收企业所期盼的规模化发展,在2018年或有望实现。
广发证券此前研报就分析称,动力电池自2014年开始实现超高速增长,至今已有四年以上历史。目前大部分动力电池厂向主机厂销售质保8年,2016年以前仍有5年质保,但考虑早期电池生产仍未成熟,假设实际使用寿命4年,系统能量密度按照每年提升约15%。经测算,2018年开始动力电池报废量将呈翻倍式增长,2018至2020年报废量分别为3.95 万吨、15.27万吨和27.73万吨,合计近50万吨。