品牌:彩色画册印刷 东莞彩色画册印刷
起订:20份
供应:99911份
发货:3天内
信息标签:东莞彩色画册印刷,供应,印刷、纸品,印刷服务
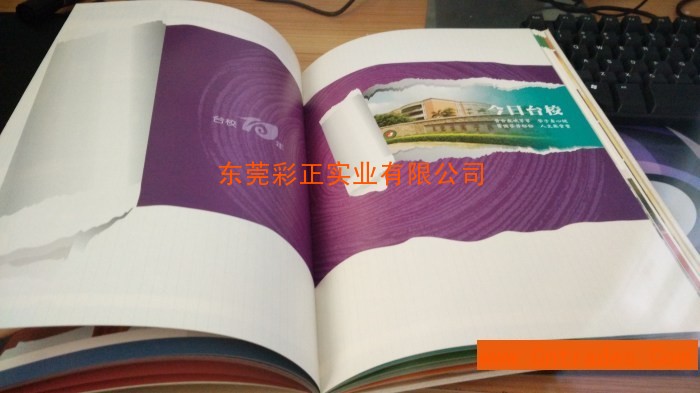
彩正实业公司,专业东莞彩色画册印刷,价格低廉,质量好,广东省包邮,外省也只需少量邮差。
彩正实业公司是一家专注纸品印刷的东莞印刷供应商,供应五金画册、招商画册、企业画册、产品宣传画册等不同行业画册印刷,价格经济实惠欢迎咨询。
彩正实业公司是东莞及至全国市场上大型的印刷品供应商之一公司配有几十位后期加工人员。胶装采用马天尼胶装龙印刷采用**的德堡对开四色印刷机和小森对开四色印刷机拥有完善的基本后续加工流程。拥有独立的画册设计印刷部、手提袋业务中心台历挂历业务中心彩卡业务中心。
**设备,高品质,高产能
彩正实业公司始终坚持技术创新和人才培训,好的人才、好的技术、好的设备才是高品质的良好基础,才是推动公司进步的主力军。
彩正实业公司推出经济型印刷解决方案为了让广大客人享受**低价的印刷服务,彩正实业公司推出了经济型画册印刷解决案,让您感觉您的画册印刷成本低谦,但又不失档次,为此我们公司采大量现金去纸厂采购国内**铜版纸,这样可以保证比相同品质的纸张比同行价格低300-600元/吨。具体的这里不作详细解说,有需要的客户请参考网站上的画册印刷报价。
服务优势质量保证:无需担心品质问题,我们设有品检部,印刷品通通经过检验后出货,所用油墨均使用国内大型**油墨厂家的,所用纸张标配金东纸业的铜版纸。
无忧退货:如客户发现有印刷品质问题,可直接联系彩正实业公司品质处理中心,为您提供便捷的服务流程。对有争议产品,将实行快捷处理,如属快印美责任,**时间安排重印或提供退货服务。必要时我司安排专人上门处理,积极听取客户意见,及时改正。
多重方案:彩正实业公司公司为顾客提供双重印刷品解决方案:a、**低价的性价比印刷品方案(主推),b、针对灯饰、家具、服装、陶瓷、光源等行业高要求的印刷品推出个性化的印刷品解决方案;尽可能的解决您的需求。
1.订货流程:我们按照您的要求定制,您提供产品的规格尺寸、材料、工艺和数量等具体要求或提供相应的产品图片;您也可以提供,Psd,Cdr,AI等格式的文件。我们给您核算报价。
2.合同签订:经双方沟通清楚后我们会出具一份订货合同给您审阅,您确认无误后签名并传真至我公司,我们便可下单安排打样或生产,并且在您指定的交货期内完成任务。
3.打样说明:签订合同后,我们可为您提供免费打数码样一次,每一份订单仅免收此订单的一次打样费用,如同一产品需多次打样,其打样费照收。打样时间3~5天。
4.付款方式:合同签订时预收30%订金,在打样确认签字后,再支付定金30%。完工后验收合格付清余款发货。
5.货运说明:所有货品均选择快递或物流发货,发货后我们会告知您发货日期及数量,货运公司及单号,查询电话等。
画册制作尺寸291×426mm(四边各含3mm出血位);中间加参考线分为2个页码;
二、标准画册成品大小:画册成品大小285×210mm;
三、画册排版方法:画册排版时,请将文字等内容放置于裁切线内5mm,画册裁切后才更美观;
四、画册样式:
横式画册(285×210mm),竖式画册(210×285mm),方型画册(210×210mm或280×280mm);
五、画册制作软件:本公司接受coreldraw、Illustrator、Freehand、Photoshop软件工具制作的文件;文字需转曲线或外框字;
六、画册格式要求:1、CorelDraw请存成CDR格式,(使用CorelDraw**之图形,请转换成位图,位图分辨率350dpi)。
2、Freehand, Illustrator请存成EPS格式(外挂之影像文件,需附图档);
3、Photoshop请存成TIF或JPG格式,文件分辨率350dpi以上。
七、画册制作文件色彩模式请设为C.M.Y.K模式。 八、线条低于0.076mm,印刷将无法显现,需设定不小于0.076mm。 九、颜色设定值不能低于8%,以免颜色无法显现。 十、颜色说明:1、不能以屏幕或打印稿的颜色来要求印刷色,填色时请勿使用专色,在制作时务必参照CMYK色值的%数来制作填色,
否则造成之色差不予退货。
2、相同文件在不同次印刷时,色彩都会有轻微差异,咖啡色、墨绿色、深紫色等,更易出现偏色问题,属正常。
3、黑色字勿使用C:100、M:100、Y:100、K:100之四色填色,四色填色总值超过250%以上的大色块,印刷时容易造成背印(粘花)。
更经济,更快,更好的服务水平
画册印刷报价、东莞画册印刷、东莞画册印刷报价**彩正
彩正实业公司专注五金画册、招商画册、企业画册、产品宣传画册,欢迎登陆彩正官网:www.kym6.com
印刷技术分享十六
在我们的包装印刷过程中,偶尔也会遇到印刷出现条痕或色彩浅淡的现象,这种被称为不下墨和墨脱辊的故障,是因包装印刷油墨体系的颜、填料发胀导致油墨整体胶化所致。
从理论的角度去解释:油墨的屈服值太高,油墨太稠而成了乳酪状。从实用的角度讲:油墨中的颜料、填料太多,才使油墨胶化或在贮存过程中水进入了油墨体系而导致部分絮凝。
长期以来,人们针对发胀或胶化采取不断搅拌墨斗中的油墨,或者在墨斗中安装一个搅拌器,也有在墨斗的油墨上放一个铁棍,将油墨推向墨斗辊,以保持包装印刷油墨的流动性。操作工大都喜欢采用中、高粘度的调墨油或稀释剂调节油墨(但这必须随调随用,否则仍会发生继续发胀或胶化)。而一些厂家则是把已发胀或胶化的油墨倒掉,更换流动性好的而又抗水强的油墨再去印刷。纵观这种故障,笔者围绕这一问题粗略地对此现象进行一些探讨。
一、油墨的胶化与酸碱的概念
包装印刷油墨的胶化问题在早期的油型(氧化干燥型及渗透干燥型)的油墨是经常会遇到的,而在溶剂型(挥发干燥型)及水性油墨中偶尔也会碰到。造成胶化的原因是非常复杂的。随着科学的发展,新材料的运用,从而才使我们加强了科学理论的研究,和对油墨组份材料质量的控制。油墨的组成结构发生了变化,随之也出现了各种弊端。油墨胶化的成因大体有如下六种:
1、油墨体系的树脂分子量过大(粘度过高);
2、固体组份太多(既使是粘度小的树脂连结料也不例外);
3、油墨体系酸值太高;
4、颜料、填料带有碱性;
5.干燥剂含量太多或选择添加的次序不当(如油墨生产前与生产后便会出现两种结果);
6、油墨体系的溶剂尤其是快干溶剂过多。
从上述六种原因可以发现:前两种是属于物理学范畴,而对于一个有经验的油墨制造者或包装印刷的操作者极易避免和容易排除的。后四种原因同属于化学(反应)范畴。我们在围绕后四种原因探索时还会发现:分散工艺的温度过高,溶剂的挥发,辅助添加剂的应用不当也可能会引起油墨有胶化的倾向。例如分子量仅有330的松香树脂在采用高色素炭黑生产溶剂性柔性决干包装印刷油墨时出现的胶化,堆版而难以上墨故障是与其强酸性的色素炭黑颜料和松香酸值有关。这都足以概括了酸[酸是亲电子的,是电子接受体(质子是给予体)]碱[碱是亲核的,是电子给予体(质子接受体)]还有所谓两性溶剂和树脂(既有质子给予体,又有质子接受体的水、醇、羧酸及硝酸纤维素等),其次还有一个不会形成氢键的脂族烃类溶剂及中性颜料和两性颜料等等都与胶化的关系早已显而易见。也就是人们常说的:颜料的酸碱特性与连结料的酸碱特性不相适应时,我们可以采用多种树脂与颜料、填料酸碱特性相适应而平衡或选择适当的溶剂而得到弥补或改善,这是常规的补救措施。
我们在属化学(反应)范畴进行探索时就会发现:在其化学计量浓度大到某一数值(严格地说是一个很窄的浓度范围)时,各种宏观性质就会发生突变。从微观角度考察,这时的油墨体系的活性分子开始发生缔合,形成胶粒大小不等的聚集体。这种聚集体就称为胶团或胶束,也称为缔合胶体。胶团的一个重要特性就是其增溶作用的结果,使原本不溶的或微溶的物质溶解度大大得到增加--俗称发胀。从而便加速了化学反应的作用。其反应的机理极有可能与连结料尤其是颜料分散过程有密切关系。
二、消除发胀,避免胶化的有效途径
除了上述所提到的原因外,油墨体系中的催干剂也能直接影响油墨在贮存过程中的粘度、增涨及颜料、填料的沉淀。例如高粘度的醇酸树脂与碱性颜料氧化锌在催干剂存在下一同研磨,在贮存过程中会促使油墨胶化和发胀。这是由于热加工过程中,游离脂肪酸类和碱性颜料起反应所致。因此,使用高粘度油墨原料制造油墨时,在研磨包程中,不应加铅、钴、锰催干剂。但在加入1%苯甲酸后可降低发胀倾向。催干剂的另一弊病是;能加速油墨在贮存过程中颜料的沉降。如以钛**制造油墨时,在研磨时加环烷酸锌,颜料易沉降而结成硬块。因而在颜料研磨前加入催干剂,便会导致油墨的贮存性差,易发胀、胶化及沉底结块。
近年来,人们在围绕包装印刷油墨的发胀、胶化及沉淀结块,提出过这样和那样的补救措施。其解决方法往往在故障出现后才引起人们的重视。这种被劫作业的方法,不仅加大了包装印刷厂家的生产成本、延误了时间,同时也带来了一定的处理难度。多年来根据油墨休系的胶化、交稠、成块的现象并找出盐基颜料与酸值较高或含有游离脂肪酸的连结料反应成皂,由于连结料本身凝聚胶化,油墨体系吸入了水份,颜料含量太高,使用的连结料与颜料不平衡(不恰当),连结料与油脂的助剂混溶性不良,高聚物连结料由酸溶结构被颜料吸收也会加速胶化等原因造成之后,一般补救的措施不外乎有如下四种方法:
1、太稠或因连结料聚合度过高形成的胶化时,加入脂族烃、酯、酮等稀释。
2、反应成皂的胶化类油墨加入松香溶于亚油中利用其高酸值物质来解除。
3、在包装印刷油墨里加入萘酸金属盐(过去常用的方法)。
4、水墨则需添加无机盐便可得到控制。
笔者针对以上所述的故障,分析油墨配方结构,筛选出市售的防胀、破胶剂的新材料加以论证后认为:伙征天扬化工厂(因家**产品)生产的一种改进型磷酸酯钛酸酯偶联剂,除具有对颜料的优良分散性能外,还有特珠的能使已发胀、胶化的包装印刷油墨“起死回生”的功效。例如在印刷过程中只需在已发胀的油墨里添加3~5%防胀、破胶剂就能使上述故障得到抑制--恢复油墨原状结构,粘度回归。根据防胀、破胶剂的特性,我们在油墨配方中只需直接添加颜料、填料的1.5~2.5%防胀破胶剂便可避免包装印刷的发胀和胶化。也可采用甲苯或二甲苯以1:1的比例与该产品先稀释后,再添加在油墨组份一起研磨分散,既能大大提高颜料的分散性,又能防止包装印刷油墨在生产、贮存、印刷过程中因发胀、胶化、沉淀而导致的条痕或色彩浅淡故障。同时还能大大提高油墨的支化度而增大墨膜的附着牢度,并能降低印刷油墨或挥发干燥型(溶剂型)印刷油墨烘烤温度及吹风量,从而有效地促进包装印刷油墨的正常印刷的流动性。
在我们的包装印刷过程中,偶尔也会遇到印刷出现条痕或色彩浅淡的现象,这种被称为不下墨和墨脱辊的故障,是因包装印刷油墨体系的颜、填料发胀导致油墨整体胶化所致。
从理论的角度去解释:油墨的屈服值太高,油墨太稠而成了乳酪状。从实用的角度讲:油墨中的颜料、填料太多,才使油墨胶化或在贮存过程中水进入了油墨体系而导致部分絮凝。
长期以来,人们针对发胀或胶化采取不断搅拌墨斗中的油墨,或者在墨斗中安装一个搅拌器,也有在墨斗的油墨上放一个铁棍,将油墨推向墨斗辊,以保持包装印刷油墨的流动性。操作工大都喜欢采用中、高粘度的调墨油或稀释剂调节油墨(但这必须随调随用,否则仍会发生继续发胀或胶化)。而一些厂家则是把已发胀或胶化的油墨倒掉,更换流动性好的而又抗水强的油墨再去印刷。纵观这种故障,笔者围绕这一问题粗略地对此现象进行一些探讨。
一、油墨的胶化与酸碱的概念
包装印刷油墨的胶化问题在早期的油型(氧化干燥型及渗透干燥型)的油墨是经常会遇到的,而在溶剂型(挥发干燥型)及水性油墨中偶尔也会碰到。造成胶化的原因是非常复杂的。随着科学的发展,新材料的运用,从而才使我们加强了科学理论的研究,和对油墨组份材料质量的控制。油墨的组成结构发生了变化,随之也出现了各种弊端。油墨胶化的成因大体有如下六种:
1、油墨体系的树脂分子量过大(粘度过高);
2、固体组份太多(既使是粘度小的树脂连结料也不例外);
3、油墨体系酸值太高;
4、颜料、填料带有碱性;
5.干燥剂含量太多或选择添加的次序不当(如油墨生产前与生产后便会出现两种结果);
6、油墨体系的溶剂尤其是快干溶剂过多。
从上述六种原因可以发现:前两种是属于物理学范畴,而对于一个有经验的油墨制造者或包装印刷的操作者极易避免和容易排除的。后四种原因同属于化学(反应)范畴。我们在围绕后四种原因探索时还会发现:分散工艺的温度过高,溶剂的挥发,辅助添加剂的应用不当也可能会引起油墨有胶化的倾向。例如分子量仅有330的松香树脂在采用高色素炭黑生产溶剂性柔性决干包装印刷油墨时出现的胶化,堆版而难以上墨故障是与其强酸性的色素炭黑颜料和松香酸值有关。这都足以概括了酸[酸是亲电子的,是电子接受体(质子是给予体)]碱[碱是亲核的,是电子给予体(质子接受体)]还有所谓两性溶剂和树脂(既有质子给予体,又有质子接受体的水、醇、羧酸及硝酸纤维素等),其次还有一个不会形成氢键的脂族烃类溶剂及中性颜料和两性颜料等等都与胶化的关系早已显而易见。也就是人们常说的:颜料的酸碱特性与连结料的酸碱特性不相适应时,我们可以采用多种树脂与颜料、填料酸碱特性相适应而平衡或选择适当的溶剂而得到弥补或改善,这是常规的补救措施。
我们在属化学(反应)范畴进行探索时就会发现:在其化学计量浓度大到某一数值(严格地说是一个很窄的浓度范围)时,各种宏观性质就会发生突变。从微观角度考察,这时的油墨体系的活性分子开始发生缔合,形成胶粒大小不等的聚集体。这种聚集体就称为胶团或胶束,也称为缔合胶体。胶团的一个重要特性就是其增溶作用的结果,使原本不溶的或微溶的物质溶解度大大得到增加--俗称发胀。从而便加速了化学反应的作用。其反应的机理极有可能与连结料尤其是颜料分散过程有密切关系。
二、消除发胀,避免胶化的有效途径
除了上述所提到的原因外,油墨体系中的催干剂也能直接影响油墨在贮存过程中的粘度、增涨及颜料、填料的沉淀。例如高粘度的醇酸树脂与碱性颜料氧化锌在催干剂存在下一同研磨,在贮存过程中会促使油墨胶化和发胀。这是由于热加工过程中,游离脂肪酸类和碱性颜料起反应所致。因此,使用高粘度油墨原料制造油墨时,在研磨包程中,不应加铅、钴、锰催干剂。但在加入1%苯甲酸后可降低发胀倾向。催干剂的另一弊病是;能加速油墨在贮存过程中颜料的沉降。如以钛**制造油墨时,在研磨时加环烷酸锌,颜料易沉降而结成硬块。因而在颜料研磨前加入催干剂,便会导致油墨的贮存性差,易发胀、胶化及沉底结块。
近年来,人们在围绕包装印刷油墨的发胀、胶化及沉淀结块,提出过这样和那样的补救措施。其解决方法往往在故障出现后才引起人们的重视。这种被劫作业的方法,不仅加大了包装印刷厂家的生产成本、延误了时间,同时也带来了一定的处理难度。多年来根据油墨休系的胶化、交稠、成块的现象并找出盐基颜料与酸值较高或含有游离脂肪酸的连结料反应成皂,由于连结料本身凝聚胶化,油墨体系吸入了水份,颜料含量太高,使用的连结料与颜料不平衡(不恰当),连结料与油脂的助剂混溶性不良,高聚物连结料由酸溶结构被颜料吸收也会加速胶化等原因造成之后,一般补救的措施不外乎有如下四种方法:
1、太稠或因连结料聚合度过高形成的胶化时,加入脂族烃、酯、酮等稀释。
2、反应成皂的胶化类油墨加入松香溶于亚油中利用其高酸值物质来解除。
3、在包装印刷油墨里加入萘酸金属盐(过去常用的方法)。
4、水墨则需添加无机盐便可得到控制。
笔者针对以上所述的故障,分析油墨配方结构,筛选出市售的防胀、破胶剂的新材料加以论证后认为:伙征天扬化工厂(因家**产品)生产的一种改进型磷酸酯钛酸酯偶联剂,除具有对颜料的优良分散性能外,还有特珠的能使已发胀、胶化的包装印刷油墨“起死回生”的功效。例如在印刷过程中只需在已发胀的油墨里添加3~5%防胀、破胶剂就能使上述故障得到抑制--恢复油墨原状结构,粘度回归。根据防胀、破胶剂的特性,我们在油墨配方中只需直接添加颜料、填料的1.5~2.5%防胀破胶剂便可避免包装印刷的发胀和胶化。也可采用甲苯或二甲苯以1:1的比例与该产品先稀释后,再添加在油墨组份一起研磨分散,既能大大提高颜料的分散性,又能防止包装印刷油墨在生产、贮存、印刷过程中因发胀、胶化、沉淀而导致的条痕或色彩浅淡故障。同时还能大大提高油墨的支化度而增大墨膜的附着牢度,并能降低印刷油墨或挥发干燥型(溶剂型)印刷油墨烘烤温度及吹风量,从而有效地促进包装印刷油墨的正常印刷的流动性。
在我们的包装印刷过程中,偶尔也会遇到印刷出现条痕或色彩浅淡的现象,这种被称为不下墨和墨脱辊的故障,是因包装印刷油墨体系的颜、填料发胀导致油墨整体胶化所致。
从理论的角度去解释:油墨的屈服值太高,油墨太稠而成了乳酪状。从实用的角度讲:油墨中的颜料、填料太多,才使油墨胶化或在贮存过程中水进入了油墨体系而导致部分絮凝。
长期以来,人们针对发胀或胶化采取不断搅拌墨斗中的油墨,或者在墨斗中安装一个搅拌器,也有在墨斗的油墨上放一个铁棍,将油墨推向墨斗辊,以保持包装印刷油墨的流动性。操作工大都喜欢采用中、高粘度的调墨油或稀释剂调节油墨(但这必须随调随用,否则仍会发生继续发胀或胶化)。而一些厂家则是把已发胀或胶化的油墨倒掉,更换流动性好的而又抗水强的油墨再去印刷。纵观这种故障,笔者围绕这一问题粗略地对此现象进行一些探讨。
一、油墨的胶化与酸碱的概念
包装印刷油墨的胶化问题在早期的油型(氧化干燥型及渗透干燥型)的油墨是经常会遇到的,而在溶剂型(挥发干燥型)及水性油墨中偶尔也会碰到。造成胶化的原因是非常复杂的。随着科学的发展,新材料的运用,从而才使我们加强了科学理论的研究,和对油墨组份材料质量的控制。油墨的组成结构发生了变化,随之也出现了各种弊端。油墨胶化的成因大体有如下六种:
1、油墨体系的树脂分子量过大(粘度过高);
2、固体组份太多(既使是粘度小的树脂连结料也不例外);
3、油墨体系酸值太高;
4、颜料、填料带有碱性;
5.干燥剂含量太多或选择添加的次序不当(如油墨生产前与生产后便会出现两种结果);
6、油墨体系的溶剂尤其是快干溶剂过多。
从上述六种原因可以发现:前两种是属于物理学范畴,而对于一个有经验的油墨制造者或包装印刷的操作者极易避免和容易排除的。后四种原因同属于化学(反应)范畴。我们在围绕后四种原因探索时还会发现:分散工艺的温度过高,溶剂的挥发,辅助添加剂的应用不当也可能会引起油墨有胶化的倾向。例如分子量仅有330的松香树脂在采用高色素炭黑生产溶剂性柔性决干包装印刷油墨时出现的胶化,堆版而难以上墨故障是与其强酸性的色素炭黑颜料和松香酸值有关。这都足以概括了酸[酸是亲电子的,是电子接受体(质子是给予体)]碱[碱是亲核的,是电子给予体(质子接受体)]还有所谓两性溶剂和树脂(既有质子给予体,又有质子接受体的水、醇、羧酸及硝酸纤维素等),其次还有一个不会形成氢键的脂族烃类溶剂及中性颜料和两性颜料等等都与胶化的关系早已显而易见。也就是人们常说的:颜料的酸碱特性与连结料的酸碱特性不相适应时,我们可以采用多种树脂与颜料、填料酸碱特性相适应而平衡或选择适当的溶剂而得到弥补或改善,这是常规的补救措施。
我们在属化学(反应)范畴进行探索时就会发现:在其化学计量浓度大到某一数值(严格地说是一个很窄的浓度范围)时,各种宏观性质就会发生突变。从微观角度考察,这时的油墨体系的活性分子开始发生缔合,形成胶粒大小不等的聚集体。这种聚集体就称为胶团或胶束,也称为缔合胶体。胶团的一个重要特性就是其增溶作用的结果,使原本不溶的或微溶的物质溶解度大大得到增加--俗称发胀。从而便加速了化学反应的作用。其反应的机理极有可能与连结料尤其是颜料分散过程有密切关系。
二、消除发胀,避免胶化的有效途径
除了上述所提到的原因外,油墨体系中的催干剂也能直接影响油墨在贮存过程中的粘度、增涨及颜料、填料的沉淀。例如高粘度的醇酸树脂与碱性颜料氧化锌在催干剂存在下一同研磨,在贮存过程中会促使油墨胶化和发胀。这是由于热加工过程中,游离脂肪酸类和碱性颜料起反应所致。因此,使用高粘度油墨原料制造油墨时,在研磨包程中,不应加铅、钴、锰催干剂。但在加入1%苯甲酸后可降低发胀倾向。催干剂的另一弊病是;能加速油墨在贮存过程中颜料的沉降。如以钛**制造油墨时,在研磨时加环烷酸锌,颜料易沉降而结成硬块。因而在颜料研磨前加入催干剂,便会导致油墨的贮存性差,易发胀、胶化及沉底结块。
近年来,人们在围绕包装印刷油墨的发胀、胶化及沉淀结块,提出过这样和那样的补救措施。其解决方法往往在故障出现后才引起人们的重视。这种被劫作业的方法,不仅加大了包装印刷厂家的生产成本、延误了时间,同时也带来了一定的处理难度。多年来根据油墨休系的胶化、交稠、成块的现象并找出盐基颜料与酸值较高或含有游离脂肪酸的连结料反应成皂,由于连结料本身凝聚胶化,油墨体系吸入了水份,颜料含量太高,使用的连结料与颜料不平衡(不恰当),连结料与油脂的助剂混溶性不良,高聚物连结料由酸溶结构被颜料吸收也会加速胶化等原因造成之后,一般补救的措施不外乎有如下四种方法:
1、太稠或因连结料聚合度过高形成的胶化时,加入脂族烃、酯、酮等稀释。
2、反应成皂的胶化类油墨加入松香溶于亚油中利用其高酸值物质来解除。
3、在包装印刷油墨里加入萘酸金属盐(过去常用的方法)。
4、水墨则需添加无机盐便可得到控制。
笔者针对以上所述的故障,分析油墨配方结构,筛选出市售的防胀、破胶剂的新材料加以论证后认为:伙征天扬化工厂(因家**产品)生产的一种改进型磷酸酯钛酸酯偶联剂,除具有对颜料的优良分散性能外,还有特珠的能使已发胀、胶化的包装印刷油墨“起死回生”的功效。例如在印刷过程中只需在已发胀的油墨里添加3~5%防胀、破胶剂就能使上述故障得到抑制--恢复油墨原状结构,粘度回归。根据防胀、破胶剂的特性,我们在油墨配方中只需直接添加颜料、填料的1.5~2.5%防胀破胶剂便可避免包装印刷的发胀和胶化。也可采用甲苯或二甲苯以1:1的比例与该产品先稀释后,再添加在油墨组份一起研磨分散,既能大大提高颜料的分散性,又能防止包装印刷油墨在生产、贮存、印刷过程中因发胀、胶化、沉淀而导致的条痕或色彩浅淡故障。同时还能大大提高油墨的支化度而增大墨膜的附着牢度,并能降低印刷油墨或挥发干燥型(溶剂型)印刷油墨烘烤温度及吹风量,从而有效地促进包装印刷油墨的正常印刷的流动性。
在我们的包装印刷过程中,偶尔也会遇到印刷出现条痕或色彩浅淡的现象,这种被称为不下墨和墨脱辊的故障,是因包装印刷油墨体系的颜、填料发胀导致油墨整体胶化所致。
从理论的角度去解释:油墨的屈服值太高,油墨太稠而成了乳酪状。从实用的角度讲:油墨中的颜料、填料太多,才使油墨胶化或在贮存过程中水进入了油墨体系而导致部分絮凝。
长期以来,人们针对发胀或胶化采取不断搅拌墨斗中的油墨,或者在墨斗中安装一个搅拌器,也有在墨斗的油墨上放一个铁棍,将油墨推向墨斗辊,以保持包装印刷油墨的流动性。操作工大都喜欢采用中、高粘度的调墨油或稀释剂调节油墨(但这必须随调随用,否则仍会发生继续发胀或胶化)。而一些厂家则是把已发胀或胶化的油墨倒掉,更换流动性好的而又抗水强的油墨再去印刷。纵观这种故障,笔者围绕这一问题粗略地对此现象进行一些探讨。
一、油墨的胶化与酸碱的概念
包装印刷油墨的胶化问题在早期的油型(氧化干燥型及渗透干燥型)的油墨是经常会遇到的,而在溶剂型(挥发干燥型)及水性油墨中偶尔也会碰到。造成胶化的原因是非常复杂的。随着科学的发展,新材料的运用,从而才使我们加强了科学理论的研究,和对油墨组份材料质量的控制。油墨的组成结构发生了变化,随之也出现了各种弊端。油墨胶化的成因大体有如下六种:
1、油墨体系的树脂分子量过大(粘度过高);
2、固体组份太多(既使是粘度小的树脂连结料也不例外);
3、油墨体系酸值太高;
4、颜料、填料带有碱性;
5.干燥剂含量太多或选择添加的次序不当(如油墨生产前与生产后便会出现两种结果);
6、油墨体系的溶剂尤其是快干溶剂过多。
从上述六种原因可以发现:前两种是属于物理学范畴,而对于一个有经验的油墨制造者或包装印刷的操作者极易避免和容易排除的。后四种原因同属于化学(反应)范畴。我们在围绕后四种原因探索时还会发现:分散工艺的温度过高,溶剂的挥发,辅助添加剂的应用不当也可能会引起油墨有胶化的倾向。例如分子量仅有330的松香树脂在采用高色素炭黑生产溶剂性柔性决干包装印刷油墨时出现的胶化,堆版而难以上墨故障是与其强酸性的色素炭黑颜料和松香酸值有关。这都足以概括了酸[酸是亲电子的,是电子接受体(质子是给予体)]碱[碱是亲核的,是电子给予体(质子接受体)]还有所谓两性溶剂和树脂(既有质子给予体,又有质子接受体的水、醇、羧酸及硝酸纤维素等),其次还有一个不会形成氢键的脂族烃类溶剂及中性颜料和两性颜料等等都与胶化的关系早已显而易见。也就是人们常说的:颜料的酸碱特性与连结料的酸碱特性不相适应时,我们可以采用多种树脂与颜料、填料酸碱特性相适应而平衡或选择适当的溶剂而得到弥补或改善,这是常规的补救措施。
我们在属化学(反应)范畴进行探索时就会发现:在其化学计量浓度大到某一数值(严格地说是一个很窄的浓度范围)时,各种宏观性质就会发生突变。从微观角度考察,这时的油墨体系的活性分子开始发生缔合,形成胶粒大小不等的聚集体。这种聚集体就称为胶团或胶束,也称为缔合胶体。胶团的一个重要特性就是其增溶作用的结果,使原本不溶的或微溶的物质溶解度大大得到增加--俗称发胀。从而便加速了化学反应的作用。其反应的机理极有可能与连结料尤其是颜料分散过程有密切关系。
二、消除发胀,避免胶化的有效途径
除了上述所提到的原因外,油墨体系中的催干剂也能直接影响油墨在贮存过程中的粘度、增涨及颜料、填料的沉淀。例如高粘度的醇酸树脂与碱性颜料氧化锌在催干剂存在下一同研磨,在贮存过程中会促使油墨胶化和发胀。这是由于热加工过程中,游离脂肪酸类和碱性颜料起反应所致。因此,使用高粘度油墨原料制造油墨时,在研磨包程中,不应加铅、钴、锰催干剂。但在加入1%苯甲酸后可降低发胀倾向。催干剂的另一弊病是;能加速油墨在贮存过程中颜料的沉降。如以钛**制造油墨时,在研磨时加环烷酸锌,颜料易沉降而结成硬块。因而在颜料研磨前加入催干剂,便会导致油墨的贮存性差,易发胀、胶化及沉底结块。
近年来,人们在围绕包装印刷油墨的发胀、胶化及沉淀结块,提出过这样和那样的补救措施。其解决方法往往在故障出现后才引起人们的重视。这种被劫作业的方法,不仅加大了包装印刷厂家的生产成本、延误了时间,同时也带来了一定的处理难度。多年来根据油墨休系的胶化、交稠、成块的现象并找出盐基颜料与酸值较高或含有游离脂肪酸的连结料反应成皂,由于连结料本身凝聚胶化,油墨体系吸入了水份,颜料含量太高,使用的连结料与颜料不平衡(不恰当),连结料与油脂的助剂混溶性不良,高聚物连结料由酸溶结构被颜料吸收也会加速胶化等原因造成之后,一般补救的措施不外乎有如下四种方法:
1、太稠或因连结料聚合度过高形成的胶化时,加入脂族烃、酯、酮等稀释。
2、反应成皂的胶化类油墨加入松香溶于亚油中利用其高酸值物质来解除。
3、在包装印刷油墨里加入萘酸金属盐(过去常用的方法)。
4、水墨则需添加无机盐便可得到控制。
笔者针对以上所述的故障,分析油墨配方结构,筛选出市售的防胀、破胶剂的新材料加以论证后认为:伙征天扬化工厂(因家**产品)生产的一种改进型磷酸酯钛酸酯偶联剂,除具有对颜料的优良分散性能外,还有特珠的能使已发胀、胶化的包装印刷油墨“起死回生”的功效。例如在印刷过程中只需在已发胀的油墨里添加3~5%防胀、破胶剂就能使上述故障得到抑制--恢复油墨原状结构,粘度回归。根据防胀、破胶剂的特性,我们在油墨配方中只需直接添加颜料、填料的1.5~2.5%防胀破胶剂便可避免包装印刷的发胀和胶化。也可采用甲苯或二甲苯以1:1的比例与该产品先稀释后,再添加在油墨组份一起研磨分散,既能大大提高颜料的分散性,又能防止包装印刷油墨在生产、贮存、印刷过程中因发胀、胶化、沉淀而导致的条痕或色彩浅淡故障。同时还能大大提高油墨的支化度而增大墨膜的附着牢度,并能降低印刷油墨或挥发干燥型(溶剂型)印刷油墨烘烤温度及吹风量,从而有效地促进包装印刷油墨的正常印刷的流动性。