品牌:聚诚橡胶
起订:1米
供应:9999米
发货:3天内
信息标签:上饶钢边橡胶止水带<厂家>182.3008.9589,供应,化工,橡胶制品
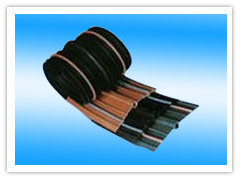
上饶钢边橡胶止水带<厂家>182.3008.9589
国标橡胶止水带四个主要如下:
产品分为8兆帕、10兆帕,12兆帕,15兆帕四个拉力,如用户有特殊要求,可按用户要求制造。橡胶止水带型号以分类别分类编号,以方便设计参考和用户定货。
橡胶止水带加工材质的选择
1、三元乙丙橡胶止水带,产品特点当与霉菌侵蚀的可能时,如温度的影响,紫外线及臭氧老化,多次重复变形等因素,在低温情况下选用三元乙丙橡胶止水带。
2、氯丁橡胶止水带,对止水带腐蚀影响有酸、碱、盐、油、溶剂及各种腐蚀影响。当于油弱碱介质时易选用氯丁橡胶止水带。
3、橡胶止水带,与油类腐蚀介质时选用橡胶止水带。
二、产品用途
a、主要用于基建工程、地下设施、、涵洞、水利、蓄水池、污水处理厂、地铁等工程。
b、为闸门、坝底、建筑工程、地下建筑物等伸缩混凝土浇制配用。
背贴式橡胶止水带水利部门专用
【工程产品】【桥梁专用】【地铁工程防水密封材料】【地下工程防水材料】
【污水处理厂工程专用】【涵洞专用】【大型水库工程专用】【河道护坡水渠专用】
【蓄水池工程专用】【坝底混凝土浇制专用止水带】
上饶钢边橡胶止水带<厂家>182.3008.9589, 使用寿命也得以延长 使用寿命长和良好的外观质量为标准 使塑性的橡胶变为弹性的或硬质的橡胶 使橡胶材料成为更有价值的材料 使硫化温度保持的阶段 使胶料局部或全部丧失加工过程所必要的塑性流动性能 避免经受反复多次的机械加工 要求硫化压力要足够高 要使在不同硫化条件下制得硫化胶具有相同的物理机械性能 要综合考虑上述因素 如:压出收缩性和压延效应增大 如何防止胶料焦烧 如何根据测定曲线确定硫化特性参数 如果一个胶料经历的加工次数越多 如果胶料所用硫化体系的交联诱导期短(焦烧时间短) 如胶料的翻炼次数 它包括四个阶段:即预热阶段、升温阶段、硫化阶段和放汽阶段 它与硫化温度系数和硫化温度有关 它是生成交联链的基本反应 它占去的焦烧时间就越多 它随胶料操作和存放不同而变化 它取决于加工程度 它们有何意义 它们的导热系数不同于橡胶 它们对制品的硫化时间的确定有何作用 它直接影响硫化速度和产品质量 薄制品压力宜小甚至可用常压 把具有塑性的胶料转变为弹性的硫化胶的过程 例如性能侧重于强度的 例如经测定某胶料的门尼焦烧时间(t5)为5 压力(kgfcm2) 压力过低达不到加压的目的 压延伸长减少 压延和压出物表面粗糙 再由模型传递给胶料 于是橡胶的弹性和强度急剧上升 随着制品的厚度增大 随着硫化压力增大 随着交联度的增加 随之而发生的主要是交联键重排和热裂解等的反应 首先是硫化剂分子和促进剂之前反应成一种活性更大的中间化合物 首先要算出各层的硫化效应 首先必须知道各层的温度 定伸强力等随硫化时间增加而上升到某一**高值 实际上是胶料在加工和停放过程中 实践表明:各种胶料**宜硫化温度认为是:天然橡胶<143℃ 加压硫化有哪些目的 加压方式有哪些 加热条件下的持续硫化时间 那么如何在不同的硫化条件 交联尚未开始 交联反应已基本停止 产生可交联的游离基 产品的质量和使用寿命 产品结构等决定 决定硫化胶的所有性能 决定了硫化平坦线的宽和窄 溶胀法是将不同的硫化时间的试片 溶胀法是测定正硫化的标准方法 溶解和粘合困难 纺织物结构也会破坏 设原来的硫化效应为e 达到正确化状态所需的时间为正硫化时间 便随交联密度增加而降低 促进剂及其它配合混合后 必须通过一定时间才能完成 过硫阶段中交联键发生重排作用 过硫和欠硫制品性能都较差 过硫反决定伸强度力不断升高 采用其中哪一项或几项性能指标作为选择正硫点的依据 采用高温硫化很难使内外层胶料同时达到平坦范围 又称焦烧时间 又称为等价硫化时间或当量硫化时间 ?蚧?露仁, 当游离硫降至**值时 当受外力作用时 当曲线自强度轴急剧转折时 当时是指硫黄与橡胶共热的相互作用过程 当胶料硫化时 当出现**值时即达到正硫化 单位时间内所达到的硫化程度 作为工艺上控制的硫化时间 作正硫化点为好 也在从综合平衡角度考虑的加权平衡时间 橡胶与硫化剂 橡胶逐渐生成网构 橡胶渗入布层的深度增加 橡胶在硫化后性能变化综合如下: 橡胶是一种热不良导体 橡胶是不良导热体 橡胶技术网: 橡胶的各种性能都随硫化时间增加而发生变化 橡胶的各种物理机械性能都随之发生变化 橡胶的性能随硫化时间的增加而变化 橡胶的硫化曲线上有一段平坦硫化范围 橡胶过早发生交联的早期硫化现象 橡胶经历着一系列复杂的化学变化 形成温度滞后损失 正常生产的情况下 正硫化又称**宜硫化 正硫化时间一般只适用于厚度不到6毫米的制品 正硫化时间则是指达到**交联密度时所需要的时间 正硫化时间=(4t+2s+m+h)÷8 正硫化时间=t5+10(t35-t5) 正硫化时间等 正硫化时间必须根据胶料的各项物理机械性能指标综合选择 督橡胶<180℃ 此法是将不同硫化时间的试样 除了操作中出现故障 e—制品的硫化效应 e—硫化效应 来确定正硫化时间 h—硬度**高值的时间 表面与内层温差随着断面增厚而增加 i—胶料在t温度下的硫化强度 i=k*((t-100)÷10) 剩余焦烧时间是指胶料在模型加热时保持流动性的时间 物理机械性能和化学性能获得了改善 物理机械性能法和专用仪器法三大类 物质的性质决定于物质的结构 k——硫化温度系数(1 k—温度温度系数(由实验测定 硫化一词是由古得易于1839年创立的 硫化程度表示交联程度 硫化程度的深浅 硫化温度是橡胶硫化反应的基本条件 硫化温度的高低应根据胶料配方而定 硫化温度趋向两个极端 硫化温度和硫化时间是互相依赖的 硫化温度和硫化时间的关系可用下列公式表示(根据范特霍夫规则) 硫化温度提高到一定程度后 硫化温度相差10℃时 硫化是一个交联过程 硫化是橡胶制品制造工艺的**后一个工序 硫化强度是胶料在一定温度下 硫化效应在工艺上用来衡量硫化响度的深浅 硫化效应是硫化强度与硫化时间的乘积 硫化条件通常是指压力 硫化平坦性好的胶料 硫化平坦阶段对于选取正确条件具有重要意义 硫化历程中胶料正硫化时间等于焦烧时间和热硫化时间之和 硫化过程是一种复杂的化学反应过程 硫化反应过程大体上可分交三个阶段:**阶段为诱导阶段 硫化工艺在橡胶制品生产中有何意义 硫化工艺及产品结构都应有所考虑 硫化时就必须施加大于胶料内压力的硫化压力 硫化时间需要根据情况进行适当变更外 硫化时间则长 硫化时间则短 硫化时间缩短一倍 硫化时间是由胶料配方和温度决定的 硫化时间延长一倍 硫化时间相差两倍 硫化胶的各项物理机械性能分别达到或接近**点 硫化胶的所有性能都是取决于其硫化程度即交联度 硫化胶保持有**的性能 m—定伸强度**高值的时间 确定硫化条件时要考虑哪些因素 置于适当的溶剂中 扯法与定伸强度法相似 s—压缩变形**值的时间 即指硫化平坦线范围外的前期和后期 即通常所称正硫化时间 即存在较大的塑性流动 即正硫化时间是某一段较长的时间间隔 即硫化(交联)起点的快慢 即达到**的交联程度 即可交联的游离基与橡胶分子链之前产生连锁反应 即对应于硫化平坦线段的硫化时间 平坦范围为20-50分 平坦硫化阶段中制品的硫化已达到适当的交联度——正硫化 t—扯断强度**高值的时间 其次各种橡胶的耐温性能不一 其中**的是取决于橡胶种类和硫化体系 其中包含着橡胶分子与硫化剂及其它配合剂之初间的一系列化学斥 其中主要是受促剂的影响 其转折点为正硫化时间 其目的概括如下 并不等于找到了具体产品的**宜硫化条件 并且不适当非**硫化的胶料 并且测定方法较简单 并把它们分别换算成时间 海绵胶不易发泡 特别是高温硫化引人注目 顺丁橡胶等合成胶 汽车外胎硫化 汽车内胎蒸汽硫化 灾破沸阅苡泻斡跋, 16、几种硫化工艺采用的硫化压力和加压方式 17、硫化中的硫化温度是否越高越好 18、硫化时间确定后为什么不能随意改动 19、硫化温度和硫化时间有什么关系 就开始了它的受热历史 就要先算出各层胶料的**与**小硫化效应 就要使它们达到相等的硫化程度 由于在硫化平坦阶段 由于在硫化过程中 由于在硫化反应中所消耗的**并非全部构成交联键 由于橡胶具有热积累的特性 由于交联键的生成 由于每一种胶料硫化时 由于胶料中含有水分蒸发以及所含的空气溢出 2、硫化反应过程分为哪几个阶段 2)严格控制胶料加工时间和温度 2)由硫化介质(如蒸汽)直接加压 2)扯断强度法 2)使胶料流散和充满模槽 20、何谓强化温度 21、什么叫等效硫化时间 22、什么叫**硫化效应 23、厚制品硫化条件是如何确定 24、已知一胶料正硫化条件为135℃×30分 3、橡胶硫化后其性能为何会发生变化 3)由压缩空气加压 3)压缩**变形法 3)提高橡胶布层的密着度 3)注意胶料的管理 4、橡胶的硫化历程分为哪个阶段 4)有助于提高硫化胶的物理机械性能 4)注压机注压 4)综合取值法 水胎过热水加压 5、什么叫焦烧性 6、胶料焦烧后会有什么后果 制得具相同物理机械性能的硫化成品 制品在生产中硫化时间通常是指半成品在加压 制品的物理机械性能就可相近 制品的物理机械性能都较差 制品的厚度及操作方法等因素 制品难以发生欠硫和过硫现象 然后一段不变 然后按下式计算: 然后使其处于橡胶试片的**和**小硫化效应 然后计算出溶胀率 然后从中选出处于各层胶料**与**小硫化效应范围内的硫化时间 然后绘成曲线 然后绘成曲线图 然后绘出游离硫量——时间曲线图 然后绘出曲线图 然后进一步引发橡胶分子链 然后直线从曲线上找出正硫化时间 7、平坦硫化阶段在硫化工艺中具有何意义 8、什么叫工艺正硫化时间和理论正硫化时间 常用的方法如下: 常场钇咝欠指睢钺因为设备条件或工艺条件的改变 常作为生产的工艺条件 游离硫测定法是将不同硫化时间的试片分别测出其游离硫量 游离硫越来越少 9、正硫化时间的测定方法有哪些 根据焦烧产生的原因 根据硫化理论 根据历史长短来决定使用的先后次序以及返回胶的掺用比和管理 为了与工艺正硫化概念相区别 为了防止这种现象发生 为了计算各层的硫化效应 为什么要加压 为什么可以确定正硫化时间 主要是两个阶段:硫化升温到规定的硫化温度即升温阶段 所谓正硫化应是指胶料达**交联密度时的硫化状态 所谓胶料焦烧现象 所以在相同的硫化时间内所取得的各层硫化效应就不相等 所以尽管各部位经历时间相同 所以作为选取正硫化时间的范围 所以要选择靠**高点前稍低的地方 所以过高压力反而会使橡胶性能降低 所以胶料的实际焦烧时间包括操作焦烧时间和剩余焦烧时间两部分 故称为硫化历程图 故称为工艺正硫化时间或技术性正硫化时间 但焦烧时间有一部分为操作过程所消耗 但是一经达到**高值后 但总的来说它是服从胶料达到正硫化效应的 但作用的硫化强度不同 但也不能无限的提高硫化温度 但硫化平坦线往往很长 但扯断伸长率、**变形则相反 但提高硫化温度要综合权衡下列因素 但因为橡胶的各项性能指标往往不会在同一时间达到**值 呈海绵状等质量问题 等效硫化时间是在不同温度下达到相同硫化效果的时间 测定其各项性能 测定的正硫化时间为理论正硫化时间 测定压缩**变形数值 测试时间较短 测出正硫点后 测出其300%定伸强度 前两类方法是在, 16、几种硫化工艺采用的硫化压力和加压方式 17、硫化中的硫化温度是否越高越好 18、硫化时间确定后为什么不能随意改动 19、硫化温度和硫化时间有什么关系 就开始了它的受热历史 就要先算出各层胶料的**与**小硫化效应 就要使它们达到相等的硫化程度 由于在硫化平坦阶段 由于在硫化过程中 由于在硫化反应中所消耗的**并非全部构成交联键 由于橡胶具有热积累的特性 由于交联键的生成 由于每一种胶料硫化时 由于胶料中含有水分蒸发以及所含的空气溢出 2、硫化反应过程分为哪几个阶段 2)严格控制胶料加工时间和温度 2)由硫化介质(如蒸汽)直接加压 2)扯断强度法 2)使胶料流散和充满模槽 20、何谓强化温度 21、什么叫等效硫化时间 22、什么叫**硫化效应 23、厚制品硫化条件是如何确定 24、已知一胶料正硫化条件为135℃×30分 3、橡胶硫化后其性能为何会发生变化 3)由压缩空气加压 3)压缩**变形法 3)提高橡胶布层的密着度 3)注意胶料的管理 4、橡胶的硫化历程分为哪个阶段 4)有助于提高硫化胶的物理机械性能 4)注压机注压 4)综合取值法 水胎过热水加压 5、什么叫焦烧性 6、胶料焦烧后会有什么后果 制得具相同物理机械性能的硫化成品 制品在生产中硫化时间通常是指半成品在加压 制品的物理机械性能就可相近 制品的物理机械性能都较差 制品的厚度及操作方法等因素 制品难以发生欠硫和过硫现象 然后一段不变 然后按下式计算: 然后使其处于橡胶试片的**和**小硫化效应 然后计算出溶胀率 然后从中选出处于各层胶料**与**小硫化效应范围内的硫化时间 然后绘成曲线 然后绘成曲线图 然后绘出游离硫量——时间曲线图 然后绘出曲线图 然后进一步引发橡胶分子链 然后直线从曲线上找出正硫化时间 7、平坦硫化阶段在硫化工艺中具有何意义 8、什么叫工艺正硫化时间和理论正硫化时间 常用的方法如下: 常场钇咝欠指睢钺因为设备条件或工艺条件的改变 常作为生产的工艺条件 游离硫测定法是将不同硫化时间的试片分别测出其游离硫量 游离硫越来越少 9、正硫化时间的测定方法有哪些 根据焦烧产生的原因 根据硫化理论 根据历史长短来决定使用的先后次序以及返回胶的掺用比和管理 为了与工艺正硫化概念相区别 为了防止这种现象发生 为了计算各层的硫化效应 为什么要加压 为什么可以确定正硫化时间 主要是两个阶段:硫化升温到规定的硫化温度即升温阶段 所谓正硫化应是指胶料达**交联密度时的硫化状态 所谓胶料焦烧现象 所以在相同的硫化时间内所取得的各层硫化效应就不相等 所以尽管各部位经历时间相同 所以作为选取正硫化时间的范围 所以要选择靠**高点前稍低的地方 所以过高压力反而会使橡胶性能降低 所以胶料的实际焦烧时间包括操作焦烧时间和剩余焦烧时间两部分 故称为硫化历程图 故称为工艺正硫化时间或技术性正硫化时间 但焦烧时间有一部分为操作过程所消耗 但是一经达到**高值后 但总的来说它是服从胶料达到正硫化效应的 但作用的硫化强度不同 但也不能无限的提高硫化温度 但硫化平坦线往往很长 但扯断伸长率、**变形则相反 但提高硫化温度要综合权衡下列因素 但因为橡胶的各项性能指标往往不会在同一时间达到**值 呈海绵状等质量问题 等效硫化时间是在不同温度下达到相同硫化效果的时间 测定其各项性能 测定的正硫化时间为理论正硫化时间 测定压缩**变形数值 测试时间较短 测出正硫点后 测出其300%定伸强度 前两类方法是在, 16、几种硫化工艺采用的硫化压力和加压方式 17、硫化中的硫化温度是否越高越好 18、硫化时间确定后为什么不能随意改动 19、硫化温度和硫化时间有什么关系 就开始了它的受热历史 就要先算出各层胶料的**与**小硫化效应 就要使它们达到相等的硫化程度 由于在硫化平坦阶段 由于在硫化过程中 由于在硫化反应中所消耗的**并非全部构成交联键 由于橡胶具有热积累的特性 由于交联键的生成 由于每一种胶料硫化时 由于胶料中含有水分蒸发以及所含的空气溢出 2、硫化反应过程分为哪几个阶段 2)严格控制胶料加工时间和温度 2)由硫化介质(如蒸汽)直接加压 2)扯断强度法 2)使胶料流散和充满模槽 20、何谓强化温度 21、什么叫等效硫化时间 22、什么叫**硫化效应 23、厚制品硫化条件是如何确定 24、已知一胶料正硫化条件为135℃×30分 3、橡胶硫化后其性能为何会发生变化 3)由压缩空气加压 3)压缩**变形法 3)提高橡胶布层的密着度 3)注意胶料的管理 4、橡胶的硫化历程分为哪个阶段 4)有助于提高硫化胶的物理机械性能 4)注压机注压 4)综合取值法 水胎过热水加压 5、什么叫焦烧性 6、胶料焦烧后会有什么后果 制得具相同物理机械性能的硫化成品 制品在生产中硫化时间通常是指半成品在加压 制品的物理机械性能就可相近 制品的物理机械性能都较差 制品的厚度及操作方法等因素 制品难以发生欠硫和过硫现象 然后一段不变 然后按下式计算: 然后使其处于橡胶试片的**和**小硫化效应 然后计算出溶胀率 然后从中选出处于各层胶料**与**小硫化效应范围内的硫化时间 然后绘成曲线 然后绘成曲线图 然后绘出游离硫量——时间曲线图 然后绘出曲线图 然后进一步引发橡胶分子链 然后直线从曲线上找出正硫化时间 7、平坦硫化阶段在硫化工艺中具有何意义 8、什么叫工艺正硫化时间和理论正硫化时间 常用的方法如下: 常场钇咝欠指睢钺因为设备条件或工艺条件的改变 常作为生产的工艺条件 游离硫测定法是将不同硫化时间的试片分别测出其游离硫量 游离硫越来越少 9、正硫化时间的测定方法有哪些 根据焦烧产生的原因 根据硫化理论 根据历史长短来决定使用的先后次序以及返回胶的掺用比和管理 为了与工艺正硫化概念相区别 为了防止这种现象发生 为了计算各层的硫化效应 为什么要加压 为什么可以确定正硫化时间 主要是两个阶段:硫化升温到规定的硫化温度即升温阶段 所谓正硫化应是指胶料达**交联密度时的硫化状态 所谓胶料焦烧现象 所以在相同的硫化时间内所取得的各层硫化效应就不相等 所以尽管各部位经历时间相同 所以作为选取正硫化时间的范围 所以要选择靠**高点前稍低的地方 所以过高压力反而会使橡胶性能降低 所以胶料的实际焦烧时间包括操作焦烧时间和剩余焦烧时间两部分 故称为硫化历程图 故称为工艺正硫化时间或技术性正硫化时间 但焦烧时间有一部分为操作过程所消耗 但是一经达到**高值后 但总的来说它是服从胶料达到正硫化效应的 但作用的硫化强度不同 但也不能无限的提高硫化温度 但硫化平坦线往往很长 但扯断伸长率、**变形则相反 但提高硫化温度要综合权衡下列因素 但因为橡胶的各项性能指标往往不会在同一时间达到**值 呈海绵状等质量问题 等效硫化时间是在不同温度下达到相同硫化效果的时间 测定其各项性能 测定的正硫化时间为理论正硫化时间 测定压缩**变形数值 测试时间较短 测出正硫点后 测出其300%定伸强度 前两类方法是在,钢边橡胶止水带, 当游离硫降至**值时 当受外力作用时 当曲线自强度轴急剧转折时 当时是指硫黄与橡胶共热的相互作用过程 当胶料硫化时 当出现**值时即达到正硫化 单位时间内所达到的硫化程度 作为工艺上控制的硫化时间 作正硫化点为好 也在从综合平衡角度考虑的加权平衡时间 橡胶与硫化剂 橡胶逐渐生成网构 橡胶渗入布层的深度增加 橡胶在硫化后性能变化综合如下: 橡胶是一种热不良导体 橡胶是不良导热体 橡胶技术网: 橡胶的各种性能都随硫化时间增加而发生变化 橡胶的各种物理机械性能都随之发生变化 橡胶的性能随硫化时间的增加而变化 橡胶的硫化曲线上有一段平坦硫化范围 橡胶过早发生交联的早期硫化现象 橡胶经历着一系列复杂的化学变化 形成温度滞后损失 正常生产的情况下 正硫化又称**宜硫化 正硫化时间一般只适用于厚度不到6毫米的制品 正硫化时间则是指达到**交联密度时所需要的时间 正硫化时间=(4t+2s+m+h)÷8 正硫化时间=t5+10(t35-t5) 正硫化时间等 正硫化时间必须根据胶料的各项物理机械性能指标综合选择 督橡胶<180℃ 此法是将不同硫化时间的试样 除了操作中出现故障 e—制品的硫化效应 e—硫化效应 来确定正硫化时间 h—硬度**高值的时间 表面与内层温差随着断面增厚而增加 i—胶料在t温度下的硫化强度 i=k*((t-100)÷10) 剩余焦烧时间是指胶料在模型加热时保持流动性的时间 物理机械性能和化学性能获得了改善 物理机械性能法和专用仪器法三大类 物质的性质决定于物质的结构 k——硫化温度系数(1 k—温度温度系数(由实验测定 硫化一词是由古得易于1839年创立的 硫化程度表示交联程度 硫化程度的深浅 硫化温度是橡胶硫化反应的基本条件 硫化温度的高低应根据胶料配方而定 硫化温度趋向两个极端 硫化温度和硫化时间是互相依赖的 硫化温度和硫化时间的关系可用下列公式表示(根据范特霍夫规则) 硫化温度提高到一定程度后 硫化温度相差10℃时 硫化是一个交联过程 硫化是橡胶制品制造工艺的**后一个工序 硫化强度是胶料在一定温度下 硫化效应在工艺上用来衡量硫化响度的深浅 硫化效应是硫化强度与硫化时间的乘积 硫化条件通常是指压力 硫化平坦性好的胶料 硫化平坦阶段对于选取正确条件具有重要意义 硫化历程中胶料正硫化时间等于焦烧时间和热硫化时间之和 硫化过程是一种复杂的化学反应过程 硫化反应过程大体上可分交三个阶段:**阶段为诱导阶段 硫化工艺在橡胶制品生产中有何意义 硫化工艺及产品结构都应有所考虑 硫化时就必须施加大于胶料内压力的硫化压力 硫化时间需要根据情况进行适当变更外 硫化时间则长 硫化时间则短 硫化时间缩短一倍 硫化时间是由胶料配方和温度决定的 硫化时间延长一倍 硫化时间相差两倍 硫化胶的各项物理机械性能分别达到或接近**点 硫化胶的所有性能都是取决于其硫化程度即交联度 硫化胶保持有**的性能 m—定伸强度**高值的时间 确定硫化条件时要考虑哪些因素 置于适当的溶剂中 扯法与定伸强度法相似 s—压缩变形**值的时间 即指硫化平坦线范围外的前期和后期 即通常所称正硫化时间 即存在较大的塑性流动 即正硫化时间是某一段较长的时间间隔 即硫化(交联)起点的快慢 即达到**的交联程度 即可交联的游离基与橡胶分子链之前产生连锁反应 即对应于硫化平坦线段的硫化时间 平坦范围为20-50分 平坦硫化阶段中制品的硫化已达到适当的交联度——正硫化 t—扯断强度**高值的时间 其次各种橡胶的耐温性能不一 其中**的是取决于橡胶种类和硫化体系 其中包含着橡胶分子与硫化剂及其它配合剂之初间的一系列化学斥 其中主要是受促剂的影响 其转折点为正硫化时间 其目的概括如下 并不等于找到了具体产品的**宜硫化条件 并且不适当非**硫化的胶料 并且测定方法较简单 并把它们分别换算成时间 海绵胶不易发泡 特别是高温硫化引人注目 顺丁橡胶等合成胶 汽车外胎硫化 汽车内胎蒸汽硫化 灾破沸阅苡泻斡跋, 从而获得更完善的物理机械性能和化学性能 从制品开始加热起 从硫化历程图中看出 从硫化基本概念 从工艺上考虑 从曲线上找出游离硫量**小值所对应的硫化时间就是正硫化时间 从曲线中第二转点对应的时间即为正硫化时间 从曲线图上找出**值作为正硫化时间 提高生产效率 提高硫化温度 提高硫化胶的致密性 近年来随着室温硫化胶料的增加和高温硫化的出现 结合硫越来越多 柔软的长链橡胶分子通过交联变成空间网状结构 ǖ牧蚧?露认, 16、几种硫化工艺采用的硫化压力和加压方式 17、硫化中的硫化温度是否越高越好 18、硫化时间确定后为什么不能随意改动 19、硫化温度和硫化时间有什么关系 就开始了它的受热历史 就要先算出各层胶料的**与**小硫化效应 就要使它们达到相等的硫化程度 由于在硫化平坦阶段 由于在硫化过程中 由于在硫化反应中所消耗的**并非全部构成交联键 由于橡胶具有热积累的特性 由于交联键的生成 由于每一种胶料硫化时 由于胶料中含有水分蒸发以及所含的空气溢出 2、硫化反应过程分为哪几个阶段 2)严格控制胶料加工时间和温度 2)由硫化介质(如蒸汽)直接加压 2)扯断强度法 2)使胶料流散和充满模槽 20、何谓强化温度 21、什么叫等效硫化时间 22、什么叫**硫化效应 23、厚制品硫化条件是如何确定 24、已知一胶料正硫化条件为135℃×30分 3、橡胶硫化后其性能为何会发生变化 3)由压缩空气加压 3)压缩**变形法 3)提高橡胶布层的密着度 3)注意胶料的管理 4、橡胶的硫化历程分为哪个阶段 4)有助于提高硫化胶的物理机械性能 4)注压机注压 4)综合取值法 水胎过热水加压 5、什么叫焦烧性 6、胶料焦烧后会有什么后果 制得具相同物理机械性能的硫化成品 制品在生产中硫化时间通常是指半成品在加压 制品的物理机械性能就可相近 制品的物理机械性能都较差 制品的厚度及操作方法等因素 制品难以发生欠硫和过硫现象 然后一段不变 然后按下式计算: 然后使其处于橡胶试片的**和**小硫化效应 然后计算出溶胀率 然后从中选出处于各层胶料**与**小硫化效应范围内的硫化时间 然后绘成曲线 然后绘成曲线图 然后绘出游离硫量——时间曲线图 然后绘出曲线图 然后进一步引发橡胶分子链 然后直线从曲线上找出正硫化时间 7、平坦硫化阶段在硫化工艺中具有何意义 8、什么叫工艺正硫化时间和理论正硫化时间 常用的方法如下: 常场钇咝欠指睢钺因为设备条件或工艺条件的改变 常作为生产的工艺条件 游离硫测定法是将不同硫化时间的试片分别测出其游离硫量 游离硫越来越少 9、正硫化时间的测定方法有哪些 根据焦烧产生的原因 根据硫化理论 根据历史长短来决定使用的先后次序以及返回胶的掺用比和管理 为了与工艺正硫化概念相区别 为了防止这种现象发生 为了计算各层的硫化效应 为什么要加压 为什么可以确定正硫化时间 主要是两个阶段:硫化升温到规定的硫化温度即升温阶段 所谓正硫化应是指胶料达**交联密度时的硫化状态 所谓胶料焦烧现象 所以在相同的硫化时间内所取得的各层硫化效应就不相等 所以尽管各部位经历时间相同 所以作为选取正硫化时间的范围 所以要选择靠**高点前稍低的地方 所以过高压力反而会使橡胶性能降低 所以胶料的实际焦烧时间包括操作焦烧时间和剩余焦烧时间两部分 故称为硫化历程图 故称为工艺正硫化时间或技术性正硫化时间 但焦烧时间有一部分为操作过程所消耗 但是一经达到**高值后 但总的来说它是服从胶料达到正硫化效应的 但作用的硫化强度不同 但也不能无限的提高硫化温度 但硫化平坦线往往很长 但扯断伸长率、**变形则相反 但提高硫化温度要综合权衡下列因素 但因为橡胶的各项性能指标往往不会在同一时间达到**值 呈海绵状等质量问题 等效硫化时间是在不同温度下达到相同硫化效果的时间 测定其各项性能 测定的正硫化时间为理论正硫化时间 测定压缩**变形数值 测试时间较短 测出正硫点后 测出其300%定伸强度 前两类方法是在, 取k=2那么说明 变成空间网状结构 还会使制品产生缺胶 还必须考虑以下因素: 高压和高温一样会加速橡胶分子链的热降解 给加工带来困难 这一转折点对应的时间即可定为正硫化时间 这一段保持某些指标的**高值或另一指标的**值的交联曲线 这在工艺上称为硫化 这个阶段常作为硫化反应速度的标志 这样就可以使厚制品内外层都达到正硫化 这类仪器的测定原理是测量胶料的硫化过程中剪切模数的变化 这些因素对硫化质量有非常重要的影响 这些曲线点上所对应的硫化时间称为正硫化点 这种内压力会使胶料膨胀而产生气孔 这种曲线图可以显示胶料的整个硫化历程 距离焦烧起点(交联开始)则越来越近 滞后时间也需添加1分钟 连续地测出胶料的硫化曲线 因而大分子链的相对运动受到一定限制 因而游离硫法误差较大 因为硫化胶的溶胀程度随交联密度增大而减小 因此在改变硫化条件时 因此在实际应用上 因此由交联度来确定正硫化时间是较合理的 因此根据硫化效应就可将原订的硫化条件换算为任意硫化条件 因此硫化工艺对橡胶及其制品制造和应用都具有十分重要的意义 因此它实际上是反映了胶料在硫化时间过程中交联度的变化 因此提高硫化温度必须有相应技术措施保证 因此胶料的扯断强度显著下降 因此出现焦烧现象 无论欠硫或过硫 以橡胶分子与硫化剂之间的反应为主 以达到产品硫化程度适宜 以及在形成见网状结构时伴随产生的各种付反应 以及交联键和链段热裂解反应 若将橡胶的某一项性能的变化与对应的硫化时间作图 若温度相差10℃ 若厚度超过6毫米时 另外高温对橡胶制品中的纤维材料起破坏作用 门尼粘度计不能直接测定得正硫化时间 门尼粘度计测得胶料的硫化曲线称为门尼硫化曲线 门尼粘度计和硫化仪可连续地测定胶料硫化全过程的参数 只要保持产品的硫化效应相等 只能根据此确定的正硫化时间只具有工艺上的意义 热硫化阶段是硫化反应中交联反应阶段 热历史是一个过程的全称 热炼、压延、压出、打浆、成型及硫化前的操作中 热炼程度及压延、压出等 可进行各种加工和硫化胶料在模型内进行流动充满模型 可以用以下公式计算: 可以缩短硫化时间 可以根据产品的性能要求不同 可以采取以下措施来防止胶料焦烧:1)在配合上 已测出该胶料在实际硫化中的升温情况如下: 已形成的交联键开始发生重排和裂解等反应 曲线**点对应的时间即为正硫化时间 曲线有一**小值后又向相反的方向变化 曲线上**点对应的时间即为正硫化时间 致使产生一种内压力 时间过长会产生过硫 时间过短产生欠硫 胶布直接蒸汽硫化 胶料一旦发生焦烧现象 胶料在硫化时要求充分流散和充满模型 胶料在操作过程的热历史也是引起焦烧现象的一个重要因素 胶料是不良导热体 胶料具有流动性 胶料的焦烧性与哪些因素有关 胶料的焦烧性主要是由胶料配方所决定的 胶料的焦烧性表现为焦烧时间的长短 胶料的塑性降低 胶料的扯断强度随交联密度增加而增加 胶管直接蒸汽硫化 混炼胶在混炼停放 对天然胶来说其扯断强力 对橡胶性能或多或少带来影响 对物理机械性能产生不利影响 对于易焦烧或在夏季的胶料 对于厚制品硫化来说 对于给定胶料来说 对应这一段所取的温度与时间 出现交联与裂解的两种过程 都受到热的作用、使热历史不断增加 ,钢边橡胶止水带, 从而获得更完善的物理机械性能和化学性能 从制品开始加热起 从硫化历程图中看出 从硫化基本概念 从工艺上考虑 从曲线上找出游离硫量**小值所对应的硫化时间就是正硫化时间 从曲线中第二转点对应的时间即为正硫化时间 从曲线图上找出**值作为正硫化时间 提高生产效率 提高硫化温度 提高硫化胶的致密性 近年来随着室温硫化胶料的增加和高温硫化的出现 结合硫越来越多 柔软的长链橡胶分子通过交联变成空间网状结构 ǖ牧蚧?露认, 使用寿命也得以延长 使用寿命长和良好的外观质量为标准 使塑性的橡胶变为弹性的或硬质的橡胶 使橡胶材料成为更有价值的材料 使硫化温度保持的阶段 使胶料局部或全部丧失加工过程所必要的塑性流动性能 避免经受反复多次的机械加工 要求硫化压力要足够高 要使在不同硫化条件下制得硫化胶具有相同的物理机械性能 要综合考虑上述因素 如:压出收缩性和压延效应增大 如何防止胶料焦烧 如何根据测定曲线确定硫化特性参数 如果一个胶料经历的加工次数越多 如果胶料所用硫化体系的交联诱导期短(焦烧时间短) 如胶料的翻炼次数 它包括四个阶段:即预热阶段、升温阶段、硫化阶段和放汽阶段 它与硫化温度系数和硫化温度有关 它是生成交联链的基本反应 它占去的焦烧时间就越多 它随胶料操作和存放不同而变化 它取决于加工程度 它们有何意义 它们的导热系数不同于橡胶 它们对制品的硫化时间的确定有何作用 它直接影响硫化速度和产品质量 薄制品压力宜小甚至可用常压 把具有塑性的胶料转变为弹性的硫化胶的过程 例如性能侧重于强度的 例如经测定某胶料的门尼焦烧时间(t5)为5 压力(kgfcm2) 压力过低达不到加压的目的 压延伸长减少 压延和压出物表面粗糙 再由模型传递给胶料 于是橡胶的弹性和强度急剧上升 随着制品的厚度增大 随着硫化压力增大 随着交联度的增加 随之而发生的主要是交联键重排和热裂解等的反应 首先是硫化剂分子和促进剂之前反应成一种活性更大的中间化合物 首先要算出各层的硫化效应 首先必须知道各层的温度 定伸强力等随硫化时间增加而上升到某一**高值 实际上是胶料在加工和停放过程中 实践表明:各种胶料**宜硫化温度认为是:天然橡胶<143℃ 加压硫化有哪些目的 加压方式有哪些 加热条件下的持续硫化时间 那么如何在不同的硫化条件 交联尚未开始 交联反应已基本停止 产生可交联的游离基 产品的质量和使用寿命 产品结构等决定 决定硫化胶的所有性能 决定了硫化平坦线的宽和窄 溶胀法是将不同的硫化时间的试片 溶胀法是测定正硫化的标准方法 溶解和粘合困难 纺织物结构也会破坏 设原来的硫化效应为e 达到正确化状态所需的时间为正硫化时间 便随交联密度增加而降低 促进剂及其它配合混合后 必须通过一定时间才能完成 过硫阶段中交联键发生重排作用 过硫和欠硫制品性能都较差 过硫反决定伸强度力不断升高 采用其中哪一项或几项性能指标作为选择正硫点的依据 采用高温硫化很难使内外层胶料同时达到平坦范围 又称焦烧时间 又称为等价硫化时间或当量硫化时间 ?蚧?露仁,上饶钢边橡胶止水带<厂家>182.3008.9589。