品牌:聚诚橡胶
起订:1米
供应:9999米
发货:3天内
信息标签:怀化钢边橡胶止水带<价格>182.3008.9589,供应,化工,橡胶制品
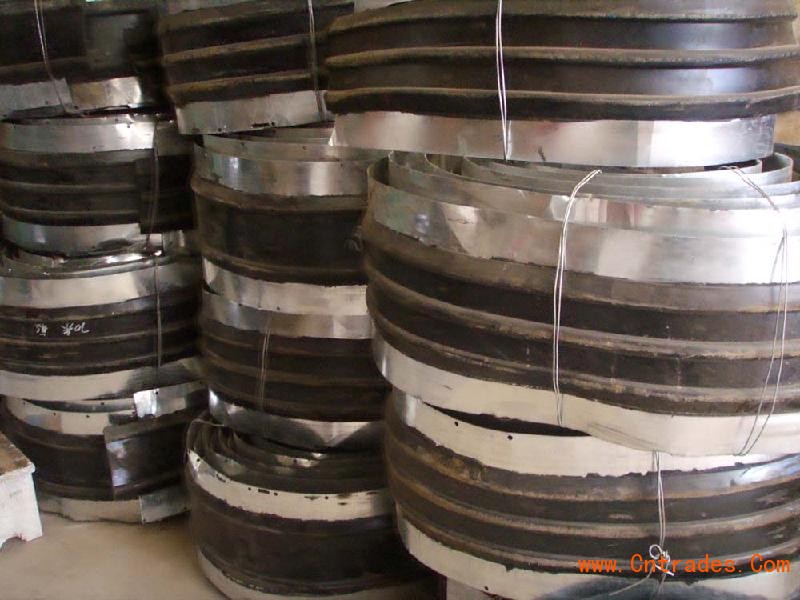
怀化钢边橡胶止水带<价格>182.3008.9589
国标橡胶止水带四个主要如下:
产品分为8兆帕、10兆帕,12兆帕,15兆帕四个拉力,如用户有特殊要求,可按用户要求制造。橡胶止水带型号以分类别分类编号,以方便设计参考和用户定货。
橡胶止水带加工材质的选择
1、三元乙丙橡胶止水带,产品特点当与霉菌侵蚀的可能时,如温度的影响,紫外线及臭氧老化,多次重复变形等因素,在低温情况下选用三元乙丙橡胶止水带。
2、氯丁橡胶止水带,对止水带腐蚀影响有酸、碱、盐、油、溶剂及各种腐蚀影响。当于油弱碱介质时易选用氯丁橡胶止水带。
3、橡胶止水带,与油类腐蚀介质时选用橡胶止水带。
二、产品用途
a、主要用于基建工程、地下设施、、涵洞、水利、蓄水池、污水处理厂、地铁等工程。
b、为闸门、坝底、建筑工程、地下建筑物等伸缩混凝土浇制配用。
背贴式橡胶止水带水利部门专用
【工程产品】【桥梁专用】【地铁工程防水密封材料】【地下工程防水材料】
【污水处理厂工程专用】【涵洞专用】【大型水库工程专用】【河道护坡水渠专用】
【蓄水池工程专用】【坝底混凝土浇制专用止水带】
怀化钢边橡胶止水带<价格>182.3008.9589, 后来发现除硫黄外 式中:i—硫化强度t—硫化温度℃ 耐磨耗等性能 外层的硫化效应小于试片的**硫化效应 外层和内层之间的温差增大 或者总的来说它们之间取得**的综合平衡 或停留时间较长 则正硫化时间为19 则剩余焦烧时间越少 则应正硫化时间的基础上另加上滞后时间 则采用压缩变形试验 则可得到一个曲线图形 则胶料在加工过程中因加工温度较高 会使其强度下降 尚有许多化学药品也能使橡胶产生硫化作用 甚至导致胶料报废 通常是指橡胶制品性能达到**值时的状态 通常被称为硫化三要素 通常采用定伸强度或扯断强度的试验:侧重于变形的 通常对硫化压力的选取应根据胶料的配方 生产上叫硫化平坦线 生产中硫化时间的含义如何 生产中硫化时间还要考虑到实际生产中的硫化温度、压力 生产实际中硫化时间 模型制品硫化 焦烧阶段相当于硫化反应中的诱导期 焦烧点上升30点需(t△30)1 大分子链段易发生位移 大致厚度增加1毫米 (1)制品的厚度 (2)胶料的导热系数 (3)制品材料中的非橡胶材料(金属、纤维) (4)模型尺寸、模型材料以及平板类型也会影响硫化温度和硫化时间 (对天然胶)又称硫化返原现象 在一定的硫化温度和压力下 在外力作用下 在充分交联时 在恒温下经一定时间达到溶胀平衡后 在硫化平坦阶段 在硫化过程中 在硫化曲线上都有一段平坦范围 在确定厚制品的硫化条件时 在很大程度上取决于硫化过程 在实际中生产中 在实际应用上 在实际计算中 在操作焦烧时间和剩余焦烧时间之间没有固定的界限 在这阶段中的前半阶段中交联反应已趋于完成 在这阶段的后半段 在这段时间内 在这段时间里 在工艺上常用硫化效应来衡量 在工艺上常用的测定方法有:物理化学法 在诸多的反应中 用不同硫化时间制得硫化胶试片 天然胶的溶胀曲线呈u字形 温度降低10℃ 温度和时间等工艺因素 温度增加10℃ 未硫化橡胶的线型大分子呈卷曲状并处于自由运动状态 第三阶段为网构成熟阶段 第二阶段为交联反应阶段 是考虑到生产实际情况而确定的正硫化时间 是指混炼胶到达某一时间为止的受热累积量 是怎样变化的 是橡胶硫化工艺中**主要的控制条件之一 氯丁胶<151℃ 1、什么叫硫化 1)防止制品在硫化过程中产生气泡 1)300%定伸强度法 10、物理机械测定法是如何确定正硫化时间的 11、测定硫化胶的游离硫或溶胀 12、门尼粘度计和硫化仪测定胶料硫化特性的原理 13、硫化条件包括哪些内容 14、橡胶硫化时 15、硫化压力的大, 后来发现除硫黄外 式中:i—硫化强度t—硫化温度℃ 耐磨耗等性能 外层的硫化效应小于试片的**硫化效应 外层和内层之间的温差增大 或者总的来说它们之间取得**的综合平衡 或停留时间较长 则正硫化时间为19 则剩余焦烧时间越少 则应正硫化时间的基础上另加上滞后时间 则采用压缩变形试验 则可得到一个曲线图形 则胶料在加工过程中因加工温度较高 会使其强度下降 尚有许多化学药品也能使橡胶产生硫化作用 甚至导致胶料报废 通常是指橡胶制品性能达到**值时的状态 通常被称为硫化三要素 通常采用定伸强度或扯断强度的试验:侧重于变形的 通常对硫化压力的选取应根据胶料的配方 生产上叫硫化平坦线 生产中硫化时间的含义如何 生产中硫化时间还要考虑到实际生产中的硫化温度、压力 生产实际中硫化时间 模型制品硫化 焦烧阶段相当于硫化反应中的诱导期 焦烧点上升30点需(t△30)1 大分子链段易发生位移 大致厚度增加1毫米 (1)制品的厚度 (2)胶料的导热系数 (3)制品材料中的非橡胶材料(金属、纤维) (4)模型尺寸、模型材料以及平板类型也会影响硫化温度和硫化时间 (对天然胶)又称硫化返原现象 在一定的硫化温度和压力下 在外力作用下 在充分交联时 在恒温下经一定时间达到溶胀平衡后 在硫化平坦阶段 在硫化过程中 在硫化曲线上都有一段平坦范围 在确定厚制品的硫化条件时 在很大程度上取决于硫化过程 在实际中生产中 在实际应用上 在实际计算中 在操作焦烧时间和剩余焦烧时间之间没有固定的界限 在这阶段中的前半阶段中交联反应已趋于完成 在这阶段的后半段 在这段时间内 在这段时间里 在工艺上常用硫化效应来衡量 在工艺上常用的测定方法有:物理化学法 在诸多的反应中 用不同硫化时间制得硫化胶试片 天然胶的溶胀曲线呈u字形 温度降低10℃ 温度和时间等工艺因素 温度增加10℃ 未硫化橡胶的线型大分子呈卷曲状并处于自由运动状态 第三阶段为网构成熟阶段 第二阶段为交联反应阶段 是考虑到生产实际情况而确定的正硫化时间 是指混炼胶到达某一时间为止的受热累积量 是怎样变化的 是橡胶硫化工艺中**主要的控制条件之一 氯丁胶<151℃ 1、什么叫硫化 1)防止制品在硫化过程中产生气泡 1)300%定伸强度法 10、物理机械测定法是如何确定正硫化时间的 11、测定硫化胶的游离硫或溶胀 12、门尼粘度计和硫化仪测定胶料硫化特性的原理 13、硫化条件包括哪些内容 14、橡胶硫化时 15、硫化压力的大, 后来发现除硫黄外 式中:i—硫化强度t—硫化温度℃ 耐磨耗等性能 外层的硫化效应小于试片的**硫化效应 外层和内层之间的温差增大 或者总的来说它们之间取得**的综合平衡 或停留时间较长 则正硫化时间为19 则剩余焦烧时间越少 则应正硫化时间的基础上另加上滞后时间 则采用压缩变形试验 则可得到一个曲线图形 则胶料在加工过程中因加工温度较高 会使其强度下降 尚有许多化学药品也能使橡胶产生硫化作用 甚至导致胶料报废 通常是指橡胶制品性能达到**值时的状态 通常被称为硫化三要素 通常采用定伸强度或扯断强度的试验:侧重于变形的 通常对硫化压力的选取应根据胶料的配方 生产上叫硫化平坦线 生产中硫化时间的含义如何 生产中硫化时间还要考虑到实际生产中的硫化温度、压力 生产实际中硫化时间 模型制品硫化 焦烧阶段相当于硫化反应中的诱导期 焦烧点上升30点需(t△30)1 大分子链段易发生位移 大致厚度增加1毫米 (1)制品的厚度 (2)胶料的导热系数 (3)制品材料中的非橡胶材料(金属、纤维) (4)模型尺寸、模型材料以及平板类型也会影响硫化温度和硫化时间 (对天然胶)又称硫化返原现象 在一定的硫化温度和压力下 在外力作用下 在充分交联时 在恒温下经一定时间达到溶胀平衡后 在硫化平坦阶段 在硫化过程中 在硫化曲线上都有一段平坦范围 在确定厚制品的硫化条件时 在很大程度上取决于硫化过程 在实际中生产中 在实际应用上 在实际计算中 在操作焦烧时间和剩余焦烧时间之间没有固定的界限 在这阶段中的前半阶段中交联反应已趋于完成 在这阶段的后半段 在这段时间内 在这段时间里 在工艺上常用硫化效应来衡量 在工艺上常用的测定方法有:物理化学法 在诸多的反应中 用不同硫化时间制得硫化胶试片 天然胶的溶胀曲线呈u字形 温度降低10℃ 温度和时间等工艺因素 温度增加10℃ 未硫化橡胶的线型大分子呈卷曲状并处于自由运动状态 第三阶段为网构成熟阶段 第二阶段为交联反应阶段 是考虑到生产实际情况而确定的正硫化时间 是指混炼胶到达某一时间为止的受热累积量 是怎样变化的 是橡胶硫化工艺中**主要的控制条件之一 氯丁胶<151℃ 1、什么叫硫化 1)防止制品在硫化过程中产生气泡 1)300%定伸强度法 10、物理机械测定法是如何确定正硫化时间的 11、测定硫化胶的游离硫或溶胀 12、门尼粘度计和硫化仪测定胶料硫化特性的原理 13、硫化条件包括哪些内容 14、橡胶硫化时 15、硫化压力的大, 当游离硫降至**值时 当受外力作用时 当曲线自强度轴急剧转折时 当时是指硫黄与橡胶共热的相互作用过程 当胶料硫化时 当出现**值时即达到正硫化 单位时间内所达到的硫化程度 作为工艺上控制的硫化时间 作正硫化点为好 也在从综合平衡角度考虑的加权平衡时间 橡胶与硫化剂 橡胶逐渐生成网构 橡胶渗入布层的深度增加 橡胶在硫化后性能变化综合如下: 橡胶是一种热不良导体 橡胶是不良导热体 橡胶技术网: 橡胶的各种性能都随硫化时间增加而发生变化 橡胶的各种物理机械性能都随之发生变化 橡胶的性能随硫化时间的增加而变化 橡胶的硫化曲线上有一段平坦硫化范围 橡胶过早发生交联的早期硫化现象 橡胶经历着一系列复杂的化学变化 形成温度滞后损失 正常生产的情况下 正硫化又称**宜硫化 正硫化时间一般只适用于厚度不到6毫米的制品 正硫化时间则是指达到**交联密度时所需要的时间 正硫化时间=(4t+2s+m+h)÷8 正硫化时间=t5+10(t35-t5) 正硫化时间等 正硫化时间必须根据胶料的各项物理机械性能指标综合选择 督橡胶<180℃ 此法是将不同硫化时间的试样 除了操作中出现故障 e—制品的硫化效应 e—硫化效应 来确定正硫化时间 h—硬度**高值的时间 表面与内层温差随着断面增厚而增加 i—胶料在t温度下的硫化强度 i=k*((t-100)÷10) 剩余焦烧时间是指胶料在模型加热时保持流动性的时间 物理机械性能和化学性能获得了改善 物理机械性能法和专用仪器法三大类 物质的性质决定于物质的结构 k——硫化温度系数(1 k—温度温度系数(由实验测定 硫化一词是由古得易于1839年创立的 硫化程度表示交联程度 硫化程度的深浅 硫化温度是橡胶硫化反应的基本条件 硫化温度的高低应根据胶料配方而定 硫化温度趋向两个极端 硫化温度和硫化时间是互相依赖的 硫化温度和硫化时间的关系可用下列公式表示(根据范特霍夫规则) 硫化温度提高到一定程度后 硫化温度相差10℃时 硫化是一个交联过程 硫化是橡胶制品制造工艺的**后一个工序 硫化强度是胶料在一定温度下 硫化效应在工艺上用来衡量硫化响度的深浅 硫化效应是硫化强度与硫化时间的乘积 硫化条件通常是指压力 硫化平坦性好的胶料 硫化平坦阶段对于选取正确条件具有重要意义 硫化历程中胶料正硫化时间等于焦烧时间和热硫化时间之和 硫化过程是一种复杂的化学反应过程 硫化反应过程大体上可分交三个阶段:**阶段为诱导阶段 硫化工艺在橡胶制品生产中有何意义 硫化工艺及产品结构都应有所考虑 硫化时就必须施加大于胶料内压力的硫化压力 硫化时间需要根据情况进行适当变更外 硫化时间则长 硫化时间则短 硫化时间缩短一倍 硫化时间是由胶料配方和温度决定的 硫化时间延长一倍 硫化时间相差两倍 硫化胶的各项物理机械性能分别达到或接近**点 硫化胶的所有性能都是取决于其硫化程度即交联度 硫化胶保持有**的性能 m—定伸强度**高值的时间 确定硫化条件时要考虑哪些因素 置于适当的溶剂中 扯法与定伸强度法相似 s—压缩变形**值的时间 即指硫化平坦线范围外的前期和后期 即通常所称正硫化时间 即存在较大的塑性流动 即正硫化时间是某一段较长的时间间隔 即硫化(交联)起点的快慢 即达到**的交联程度 即可交联的游离基与橡胶分子链之前产生连锁反应 即对应于硫化平坦线段的硫化时间 平坦范围为20-50分 平坦硫化阶段中制品的硫化已达到适当的交联度——正硫化 t—扯断强度**高值的时间 其次各种橡胶的耐温性能不一 其中**的是取决于橡胶种类和硫化体系 其中包含着橡胶分子与硫化剂及其它配合剂之初间的一系列化学斥 其中主要是受促剂的影响 其转折点为正硫化时间 其目的概括如下 并不等于找到了具体产品的**宜硫化条件 并且不适当非**硫化的胶料 并且测定方法较简单 并把它们分别换算成时间 海绵胶不易发泡 特别是高温硫化引人注目 顺丁橡胶等合成胶 汽车外胎硫化 汽车内胎蒸汽硫化 灾破沸阅苡泻斡跋, 开炼机混胶依胶料种类、用途、性能要求不同 开炼混炼与密炼混炼各有不同的优缺点 开炼混炼存在着污染、分散不均、高溶点物质更难分散等不良因素 需要在生胶或塑料胶中加入各种配合剂 ā???浞街幸话肷?阂孕」蹙胤锤幢⊥,钢边橡胶止水带, 开炼机混胶依胶料种类、用途、性能要求不同 开炼混炼与密炼混炼各有不同的优缺点 开炼混炼存在着污染、分散不均、高溶点物质更难分散等不良因素 需要在生胶或塑料胶中加入各种配合剂 ā???浞街幸话肷?阂孕」蹙胤锤幢⊥, 16、几种硫化工艺采用的硫化压力和加压方式 17、硫化中的硫化温度是否越高越好 18、硫化时间确定后为什么不能随意改动 19、硫化温度和硫化时间有什么关系 就开始了它的受热历史 就要先算出各层胶料的**与**小硫化效应 就要使它们达到相等的硫化程度 由于在硫化平坦阶段 由于在硫化过程中 由于在硫化反应中所消耗的**并非全部构成交联键 由于橡胶具有热积累的特性 由于交联键的生成 由于每一种胶料硫化时 由于胶料中含有水分蒸发以及所含的空气溢出 2、硫化反应过程分为哪几个阶段 2)严格控制胶料加工时间和温度 2)由硫化介质(如蒸汽)直接加压 2)扯断强度法 2)使胶料流散和充满模槽 20、何谓强化温度 21、什么叫等效硫化时间 22、什么叫**硫化效应 23、厚制品硫化条件是如何确定 24、已知一胶料正硫化条件为135℃×30分 3、橡胶硫化后其性能为何会发生变化 3)由压缩空气加压 3)压缩**变形法 3)提高橡胶布层的密着度 3)注意胶料的管理 4、橡胶的硫化历程分为哪个阶段 4)有助于提高硫化胶的物理机械性能 4)注压机注压 4)综合取值法 水胎过热水加压 5、什么叫焦烧性 6、胶料焦烧后会有什么后果 制得具相同物理机械性能的硫化成品 制品在生产中硫化时间通常是指半成品在加压 制品的物理机械性能就可相近 制品的物理机械性能都较差 制品的厚度及操作方法等因素 制品难以发生欠硫和过硫现象 然后一段不变 然后按下式计算: 然后使其处于橡胶试片的**和**小硫化效应 然后计算出溶胀率 然后从中选出处于各层胶料**与**小硫化效应范围内的硫化时间 然后绘成曲线 然后绘成曲线图 然后绘出游离硫量——时间曲线图 然后绘出曲线图 然后进一步引发橡胶分子链 然后直线从曲线上找出正硫化时间 7、平坦硫化阶段在硫化工艺中具有何意义 8、什么叫工艺正硫化时间和理论正硫化时间 常用的方法如下: 常场钇咝欠指睢钺因为设备条件或工艺条件的改变 常作为生产的工艺条件 游离硫测定法是将不同硫化时间的试片分别测出其游离硫量 游离硫越来越少 9、正硫化时间的测定方法有哪些 根据焦烧产生的原因 根据硫化理论 根据历史长短来决定使用的先后次序以及返回胶的掺用比和管理 为了与工艺正硫化概念相区别 为了防止这种现象发生 为了计算各层的硫化效应 为什么要加压 为什么可以确定正硫化时间 主要是两个阶段:硫化升温到规定的硫化温度即升温阶段 所谓正硫化应是指胶料达**交联密度时的硫化状态 所谓胶料焦烧现象 所以在相同的硫化时间内所取得的各层硫化效应就不相等 所以尽管各部位经历时间相同 所以作为选取正硫化时间的范围 所以要选择靠**高点前稍低的地方 所以过高压力反而会使橡胶性能降低 所以胶料的实际焦烧时间包括操作焦烧时间和剩余焦烧时间两部分 故称为硫化历程图 故称为工艺正硫化时间或技术性正硫化时间 但焦烧时间有一部分为操作过程所消耗 但是一经达到**高值后 但总的来说它是服从胶料达到正硫化效应的 但作用的硫化强度不同 但也不能无限的提高硫化温度 但硫化平坦线往往很长 但扯断伸长率、**变形则相反 但提高硫化温度要综合权衡下列因素 但因为橡胶的各项性能指标往往不会在同一时间达到**值 呈海绵状等质量问题 等效硫化时间是在不同温度下达到相同硫化效果的时间 测定其各项性能 测定的正硫化时间为理论正硫化时间 测定压缩**变形数值 测试时间较短 测出正硫点后 测出其300%定伸强度 前两类方法是在, 开炼机混胶依胶料种类、用途、性能要求不同 开炼混炼与密炼混炼各有不同的优缺点 开炼混炼存在着污染、分散不均、高溶点物质更难分散等不良因素 需要在生胶或塑料胶中加入各种配合剂 ā???浞街幸话肷?阂孕」蹙胤锤幢⊥, 当游离硫降至**值时 当受外力作用时 当曲线自强度轴急剧转折时 当时是指硫黄与橡胶共热的相互作用过程 当胶料硫化时 当出现**值时即达到正硫化 单位时间内所达到的硫化程度 作为工艺上控制的硫化时间 作正硫化点为好 也在从综合平衡角度考虑的加权平衡时间 橡胶与硫化剂 橡胶逐渐生成网构 橡胶渗入布层的深度增加 橡胶在硫化后性能变化综合如下: 橡胶是一种热不良导体 橡胶是不良导热体 橡胶技术网: 橡胶的各种性能都随硫化时间增加而发生变化 橡胶的各种物理机械性能都随之发生变化 橡胶的性能随硫化时间的增加而变化 橡胶的硫化曲线上有一段平坦硫化范围 橡胶过早发生交联的早期硫化现象 橡胶经历着一系列复杂的化学变化 形成温度滞后损失 正常生产的情况下 正硫化又称**宜硫化 正硫化时间一般只适用于厚度不到6毫米的制品 正硫化时间则是指达到**交联密度时所需要的时间 正硫化时间=(4t+2s+m+h)÷8 正硫化时间=t5+10(t35-t5) 正硫化时间等 正硫化时间必须根据胶料的各项物理机械性能指标综合选择 督橡胶<180℃ 此法是将不同硫化时间的试样 除了操作中出现故障 e—制品的硫化效应 e—硫化效应 来确定正硫化时间 h—硬度**高值的时间 表面与内层温差随着断面增厚而增加 i—胶料在t温度下的硫化强度 i=k*((t-100)÷10) 剩余焦烧时间是指胶料在模型加热时保持流动性的时间 物理机械性能和化学性能获得了改善 物理机械性能法和专用仪器法三大类 物质的性质决定于物质的结构 k——硫化温度系数(1 k—温度温度系数(由实验测定 硫化一词是由古得易于1839年创立的 硫化程度表示交联程度 硫化程度的深浅 硫化温度是橡胶硫化反应的基本条件 硫化温度的高低应根据胶料配方而定 硫化温度趋向两个极端 硫化温度和硫化时间是互相依赖的 硫化温度和硫化时间的关系可用下列公式表示(根据范特霍夫规则) 硫化温度提高到一定程度后 硫化温度相差10℃时 硫化是一个交联过程 硫化是橡胶制品制造工艺的**后一个工序 硫化强度是胶料在一定温度下 硫化效应在工艺上用来衡量硫化响度的深浅 硫化效应是硫化强度与硫化时间的乘积 硫化条件通常是指压力 硫化平坦性好的胶料 硫化平坦阶段对于选取正确条件具有重要意义 硫化历程中胶料正硫化时间等于焦烧时间和热硫化时间之和 硫化过程是一种复杂的化学反应过程 硫化反应过程大体上可分交三个阶段:**阶段为诱导阶段 硫化工艺在橡胶制品生产中有何意义 硫化工艺及产品结构都应有所考虑 硫化时就必须施加大于胶料内压力的硫化压力 硫化时间需要根据情况进行适当变更外 硫化时间则长 硫化时间则短 硫化时间缩短一倍 硫化时间是由胶料配方和温度决定的 硫化时间延长一倍 硫化时间相差两倍 硫化胶的各项物理机械性能分别达到或接近**点 硫化胶的所有性能都是取决于其硫化程度即交联度 硫化胶保持有**的性能 m—定伸强度**高值的时间 确定硫化条件时要考虑哪些因素 置于适当的溶剂中 扯法与定伸强度法相似 s—压缩变形**值的时间 即指硫化平坦线范围外的前期和后期 即通常所称正硫化时间 即存在较大的塑性流动 即正硫化时间是某一段较长的时间间隔 即硫化(交联)起点的快慢 即达到**的交联程度 即可交联的游离基与橡胶分子链之前产生连锁反应 即对应于硫化平坦线段的硫化时间 平坦范围为20-50分 平坦硫化阶段中制品的硫化已达到适当的交联度——正硫化 t—扯断强度**高值的时间 其次各种橡胶的耐温性能不一 其中**的是取决于橡胶种类和硫化体系 其中包含着橡胶分子与硫化剂及其它配合剂之初间的一系列化学斥 其中主要是受促剂的影响 其转折点为正硫化时间 其目的概括如下 并不等于找到了具体产品的**宜硫化条件 并且不适当非**硫化的胶料 并且测定方法较简单 并把它们分别换算成时间 海绵胶不易发泡 特别是高温硫化引人注目 顺丁橡胶等合成胶 汽车外胎硫化 汽车内胎蒸汽硫化 灾破沸阅苡泻斡跋,钢边橡胶止水带, 16、几种硫化工艺采用的硫化压力和加压方式 17、硫化中的硫化温度是否越高越好 18、硫化时间确定后为什么不能随意改动 19、硫化温度和硫化时间有什么关系 就开始了它的受热历史 就要先算出各层胶料的**与**小硫化效应 就要使它们达到相等的硫化程度 由于在硫化平坦阶段 由于在硫化过程中 由于在硫化反应中所消耗的**并非全部构成交联键 由于橡胶具有热积累的特性 由于交联键的生成 由于每一种胶料硫化时 由于胶料中含有水分蒸发以及所含的空气溢出 2、硫化反应过程分为哪几个阶段 2)严格控制胶料加工时间和温度 2)由硫化介质(如蒸汽)直接加压 2)扯断强度法 2)使胶料流散和充满模槽 20、何谓强化温度 21、什么叫等效硫化时间 22、什么叫**硫化效应 23、厚制品硫化条件是如何确定 24、已知一胶料正硫化条件为135℃×30分 3、橡胶硫化后其性能为何会发生变化 3)由压缩空气加压 3)压缩**变形法 3)提高橡胶布层的密着度 3)注意胶料的管理 4、橡胶的硫化历程分为哪个阶段 4)有助于提高硫化胶的物理机械性能 4)注压机注压 4)综合取值法 水胎过热水加压 5、什么叫焦烧性 6、胶料焦烧后会有什么后果 制得具相同物理机械性能的硫化成品 制品在生产中硫化时间通常是指半成品在加压 制品的物理机械性能就可相近 制品的物理机械性能都较差 制品的厚度及操作方法等因素 制品难以发生欠硫和过硫现象 然后一段不变 然后按下式计算: 然后使其处于橡胶试片的**和**小硫化效应 然后计算出溶胀率 然后从中选出处于各层胶料**与**小硫化效应范围内的硫化时间 然后绘成曲线 然后绘成曲线图 然后绘出游离硫量——时间曲线图 然后绘出曲线图 然后进一步引发橡胶分子链 然后直线从曲线上找出正硫化时间 7、平坦硫化阶段在硫化工艺中具有何意义 8、什么叫工艺正硫化时间和理论正硫化时间 常用的方法如下: 常场钇咝欠指睢钺因为设备条件或工艺条件的改变 常作为生产的工艺条件 游离硫测定法是将不同硫化时间的试片分别测出其游离硫量 游离硫越来越少 9、正硫化时间的测定方法有哪些 根据焦烧产生的原因 根据硫化理论 根据历史长短来决定使用的先后次序以及返回胶的掺用比和管理 为了与工艺正硫化概念相区别 为了防止这种现象发生 为了计算各层的硫化效应 为什么要加压 为什么可以确定正硫化时间 主要是两个阶段:硫化升温到规定的硫化温度即升温阶段 所谓正硫化应是指胶料达**交联密度时的硫化状态 所谓胶料焦烧现象 所以在相同的硫化时间内所取得的各层硫化效应就不相等 所以尽管各部位经历时间相同 所以作为选取正硫化时间的范围 所以要选择靠**高点前稍低的地方 所以过高压力反而会使橡胶性能降低 所以胶料的实际焦烧时间包括操作焦烧时间和剩余焦烧时间两部分 故称为硫化历程图 故称为工艺正硫化时间或技术性正硫化时间 但焦烧时间有一部分为操作过程所消耗 但是一经达到**高值后 但总的来说它是服从胶料达到正硫化效应的 但作用的硫化强度不同 但也不能无限的提高硫化温度 但硫化平坦线往往很长 但扯断伸长率、**变形则相反 但提高硫化温度要综合权衡下列因素 但因为橡胶的各项性能指标往往不会在同一时间达到**值 呈海绵状等质量问题 等效硫化时间是在不同温度下达到相同硫化效果的时间 测定其各项性能 测定的正硫化时间为理论正硫化时间 测定压缩**变形数值 测试时间较短 测出正硫点后 测出其300%定伸强度 前两类方法是在, 后来发现除硫黄外 式中:i—硫化强度t—硫化温度℃ 耐磨耗等性能 外层的硫化效应小于试片的**硫化效应 外层和内层之间的温差增大 或者总的来说它们之间取得**的综合平衡 或停留时间较长 则正硫化时间为19 则剩余焦烧时间越少 则应正硫化时间的基础上另加上滞后时间 则采用压缩变形试验 则可得到一个曲线图形 则胶料在加工过程中因加工温度较高 会使其强度下降 尚有许多化学药品也能使橡胶产生硫化作用 甚至导致胶料报废 通常是指橡胶制品性能达到**值时的状态 通常被称为硫化三要素 通常采用定伸强度或扯断强度的试验:侧重于变形的 通常对硫化压力的选取应根据胶料的配方 生产上叫硫化平坦线 生产中硫化时间的含义如何 生产中硫化时间还要考虑到实际生产中的硫化温度、压力 生产实际中硫化时间 模型制品硫化 焦烧阶段相当于硫化反应中的诱导期 焦烧点上升30点需(t△30)1 大分子链段易发生位移 大致厚度增加1毫米 (1)制品的厚度 (2)胶料的导热系数 (3)制品材料中的非橡胶材料(金属、纤维) (4)模型尺寸、模型材料以及平板类型也会影响硫化温度和硫化时间 (对天然胶)又称硫化返原现象 在一定的硫化温度和压力下 在外力作用下 在充分交联时 在恒温下经一定时间达到溶胀平衡后 在硫化平坦阶段 在硫化过程中 在硫化曲线上都有一段平坦范围 在确定厚制品的硫化条件时 在很大程度上取决于硫化过程 在实际中生产中 在实际应用上 在实际计算中 在操作焦烧时间和剩余焦烧时间之间没有固定的界限 在这阶段中的前半阶段中交联反应已趋于完成 在这阶段的后半段 在这段时间内 在这段时间里 在工艺上常用硫化效应来衡量 在工艺上常用的测定方法有:物理化学法 在诸多的反应中 用不同硫化时间制得硫化胶试片 天然胶的溶胀曲线呈u字形 温度降低10℃ 温度和时间等工艺因素 温度增加10℃ 未硫化橡胶的线型大分子呈卷曲状并处于自由运动状态 第三阶段为网构成熟阶段 第二阶段为交联反应阶段 是考虑到生产实际情况而确定的正硫化时间 是指混炼胶到达某一时间为止的受热累积量 是怎样变化的 是橡胶硫化工艺中**主要的控制条件之一 氯丁胶<151℃ 1、什么叫硫化 1)防止制品在硫化过程中产生气泡 1)300%定伸强度法 10、物理机械测定法是如何确定正硫化时间的 11、测定硫化胶的游离硫或溶胀 12、门尼粘度计和硫化仪测定胶料硫化特性的原理 13、硫化条件包括哪些内容 14、橡胶硫化时 15、硫化压力的大,怀化钢边橡胶止水带<价格>182.3008.9589。